
An electric motor is an electrical machine that converts electrical energy into mechanical energy. Most electric motors operate through the interaction between the motor's magnetic field and electric current in a wire winding to generate force in the form of torque applied on the motor's shaft. Electric motors can be powered by direct current (DC) sources, such as from batteries, or rectifiers, or by alternating current (AC) sources, such as a power grid, inverters or electrical generators. An electric generator is mechanically identical to an electric motor, but operates with a reversed flow of power, converting mechanical energy into electrical energy.

In electrical engineering, the armature is the winding of an electric machine which carries alternating current. The armature windings conduct AC even on DC machines, due to the commutator action or due to electronic commutation, as in brushless DC motors. The armature can be on either the rotor or the stator, depending on the type of electric machine.
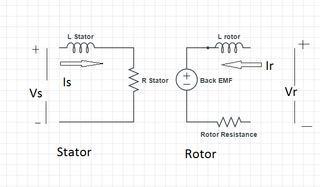
An armature controlled DC motor is a direct current (DC) motor that uses a permanent magnet driven by the armature coils only.

An axial flux motor is a geometry of electric motor construction where the gap between the rotor and stator, and therefore the direction of magnetic flux between the two, is aligned parallel with the axis of rotation, rather than radially as with the concentric cylindrical geometry of the more common radial gap motor.

Barlow's wheel was an early demonstration of a homopolar motor, designed and built by English mathematician and physicist, Peter Barlow in 1822. It consists of a star-shaped wheel free to turn suspended over a trough of the liquid metal mercury, with the points dipping into the mercury, between the poles of a horseshoe magnet. A DC electric current passes from the hub of the wheel, through the wheel into the mercury and out through an electrical contact dipping into the mercury. The Lorentz force of the magnetic field on the moving charges in the wheel causes the wheel to rotate. The presence of serrations on the wheel is unnecessary and the apparatus will work with a round metal disk, usually made of copper."The points of the wheel, R, dip into mercury contained in a groove hollowed in the stand. A more rapid revolution will be obtained if a small electro-magnet be substituted for a steel magnet, as is shown in the cut. The electro-magnet is fixed to the stand, and included in the circuit with the spur-wheel, so that the current flows through them in succession. Hence the direction of the rotation will not be changed by reversing that of the current; since the polarity of the electromagnet will also be reversed."(Excerpt taken from the 1842 edition of the Manual of Magnetism, page 94)
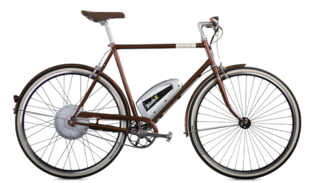
BionX was a Canadian maker of electric motors for bicycles as well as bicycle retrofit kits, operating from 1998-2018, originally named EPS.
A bipolar electric motor is an electric motor with only two poles to its stationary field. They are an example of the simple brushed DC motor, with a commutator. This field may be generated by either a permanent magnet or a field coil.

Braking choppers, sometimes also referred to as braking units, are used in the DC voltage intermediate circuits of frequency converters to control voltage when the load feeds energy back to the intermediate circuit. This arises, for example, when a magnetized motor is being rotated by an overhauling load and so functions as a generator feeding power to the DC voltage intermediate circuit. They are an application of the chopper principle, using on-off control of a switching device.

A brush or carbon brush is an electrical contact which conducts current between stationary wires and moving parts, most commonly in a rotating shaft. Typical applications include electric motors, alternators and electric generators. The lifespan of a carbon brush depends on how much the motor is used, and how much power is put through the motor.

A brushless DC electric motor, also known as an electronically commutated motor or synchronous DC motor, is a synchronous motor using a direct current (DC) electric power supply. It uses an electronic closed loop controller to switch DC currents to the motor windings producing magnetic fields which effectively rotate in space and which the permanent magnet rotor follows. The controller adjusts the phase and amplitude of the DC current pulses to control the speed and torque of the motor. This control system is an alternative to the mechanical commutator (brushes) used in many conventional electric motors.

Anwar Chitayat is the founder and former CEO and chairman of Anorad Corp., which was acquired in 1998 by Rockwell Automation. Mr. Chitayat holds over 95 patents in Electronics, Semiconductors and Automation including Nanotechnology, Interferometry and Linear motors. His achievements in High technology were honored by SEMI at their highest honor for Lifetime Achievement, reserved for individuals who repeatedly enable and lead the technology industry throughout their professional career. In the year 1997, Anwar was awarded the Entrepreneur of the year award by Ernst and Young, and in the year 2009, Anwar was inducted to Long Island Hall of Fame for his impacts on science and technology on Long Island.

First conceived by A.heyland in 1894 and B.A. Behrend in 1895, the circle diagram is the graphical representation of the performance of the electrical machine drawn in terms of the locus of the machine's input voltage and current. The circle diagram can be drawn for alternators, synchronous motors, transformers, induction motors. The Heyland diagram is an approximate representation of circle diagram applied to induction motors, which assumes that stator input voltage, rotor resistance and rotor reactance are constant and stator resistance and core loss are zero. Another common circle diagram form is as described in the two constant air-gap induction motor images shown here, where,Rs, Xs: Stator resistance and leakage reactance Rr', Xr', s: Rotor resistance and leakage reactance referred to the stator and rotor slip Rc, Xm, : Core and mechanical losses, magnetization reactance Vs, Impressed stator voltage I0 = OO', IBL = OA, I1 =OV: No load current, blocked rotor current, operating current Φ0, ΦBL : No load angle, blocked rotor angle Pmax, sPmax, PFmax, Tmax, sTmax: Maximum output power & related slip, maximum power factor, maximum torque & related slip η1, s1, PF1, Φ1,: Efficiency, slip, power factor, PF angle at operating current AB: Represents rotor power input, which divided by synchronous speed equals starting torque.

A coilgun, also known as a Gauss rifle, is a type of mass driver consisting of one or more coils used as electromagnets in the configuration of a linear motor that accelerate a ferromagnetic or conducting projectile to high velocity. In almost all coilgun configurations, the coils and the gun barrel are arranged on a common axis. A coilgun is not a rifle as the barrel is smoothbore. The name "Gauss" is in reference to Carl Friedrich Gauss, who formulated mathematical descriptions of the magnetic effect used by magnetic accelerator cannons.

A commutator is a rotary electrical switch in certain types of electric motors and electrical generators that periodically reverses the current direction between the rotor and the external circuit. It consists of a cylinder composed of multiple metal contact segments on the rotating armature of the machine. Two or more electrical contacts called "brushes" made of a soft conductive material like carbon press against the commutator, making sliding contact with successive segments of the commutator as it rotates. The windings on the armature are connected to the commutator segments.

A compensation winding in a DC shunt motor is a winding in the field pole face plate that carries armature current to reduce stator field distortion. Its purpose is to reduce brush arcing and erosion in DC motors that are operated with weak fields, variable heavy loads or reversing operation such as steel-mill motors. When flux from the armature current is about equal to the flux from the field current, the flux at the field pole plate is shifted. Under a fixed load, there is an optimal commutation point for the brushes that minimizes arcing and erosion of the brushes. When the ratio of armature flux to field flux varies greatly or reverses, the optimum commutation point shifts as result of the varying flux at the pole face plate. The result is arcing of the brushes. By adding a compensating winding in the pole face plate that carries armature current in the opposite direction of current in the adjacent armature windings, the position of the flux at the pole face plate can be restored to the position it would have with zero armature current. The main drawback of a compensation winding is the expense.

A DC motor is any of a class of rotary electrical motors that converts direct current electrical energy into mechanical energy. The most common types rely on the forces produced by magnetic fields. Nearly all types of DC motors have some internal mechanism, either electromechanical or electronic, to periodically change the direction of current in part of the motor.

A drum motor is a geared motor drive enclosed within a steel shell providing a single component driving pulley for conveyor belts.

An electrically powered spacecraft propulsion system uses electrical, and possibly also magnetic fields, to change the velocity of a spacecraft. Most of these kinds of spacecraft propulsion systems work by electrically expelling propellant at high speed.

Fleming's left-hand rule for electric motors is one of a pair of visual mnemonics, the other being Fleming's right-hand rule. They were originated by John Ambrose Fleming, in the late 19th century, as a simple way of working out the direction of motion in an electric motor, or the direction of electric current in an electric generator.

Front electric sustainer (FES) is a propulsion system for gliders that uses an electric motor powered by batteries and a foldable propeller. It is produced by LZ Design d.o.o. in Logatec, Slovenia.
A growler is an electricity device used for testing insulation of a motor for shorted coils. A growler consists of a coil of wire wrapped around an iron core and connected to a source of alternating current. When placed on the armature or stator core of a motor the growler acts as the primary of a transformer and the armature coils act as the secondary. A "feeler", a thin strip of steel can be used as the short detector.

A high performance positioning system (HPPS) is a type of positioning system consisting of a piece of electromechanics equipment that is capable of moving an object in a three-dimensional space within a work envelope. Positioning could be done point to point or along a desired path of motion. Position is typically defined in six degrees of freedom, including linear, in an x,y,z cartesian coordinate system, and angular orientation of yaw, pitch, roll. HPPS are used in many manufacturing processes to move an object smoothly and accurately in six degrees of freedom, along a desired path, at a desired orientation, with high acceleration, high deceleration, high velocity and low settling time. It is designed to quickly stop its motion and accurately place the moving object at its desired final position and orientation with minimal jittering.

A homopolar motor is a direct current electric motor with two magnetic poles, the conductors of which always cut unidirectional lines of magnetic flux by rotating a conductor around a fixed axis so that the conductor is at right angles to a static magnetic field. The resulting force being continuous in one direction, the homopolar motor needs no commutator but still requires slip rings. The name homopolar indicates that the electrical polarity of the conductor and the magnetic field poles do not change.
Houghton International is a British electro mechanical engineering company operating globally in the repair, maintenance and life extension of rotating electrical machines. Its primary market sectors are power generation, renewables, industrial, water, oil and gas, marine and rail.

The inchworm motor is a device that uses piezoelectric actuators to move a shaft with nanometer precision.

An induction motor or asynchronous motor is an AC electric motor in which the electric current in the rotor needed to produce torque is obtained by electromagnetic induction from the magnetic field of the stator winding. An induction motor can therefore be made without electrical connections to the rotor. An induction motor's rotor can be either wound type or squirrel-cage type.

An induction regulator is an alternating current electrical machine, somewhat similar to an induction motor, which can provide a continuously variable output voltage. The induction regulator was an early device used to control the voltage of electric networks. Since the 1930s it has been replaced in distribution network applications by the tap transformer. Its usage is now mostly confined to electrical laboratories, electrochemical processes and arc welding. With minor variations, its setup can be used as a phase-shifting power transformer.

An internal fan-cooled electric motor is a self cooling electric motor. Fan cooled motors feature an axial fan attached to the rotor of the motor that spins with the motor, providing increased airflow to the motor's internal and external parts which aids in cooling.

The Lavet-type stepping motor has widespread use as a drive in electro-mechanical clocks and is a special kind of single-phase stepping motor. Both analog and stepped-movement quartz clocks use the Lavet-type stepping motor. Through miniaturization, it can be used in wristwatches and requires very little power, making a battery last for many years. The French engineer Marius Lavet is known as the inventor for this kind of drives and described it in 1936 in his patent application FR823395.

A linear motor is an electric motor that has had its stator and rotor "unrolled" thus instead of producing a torque (rotation) it produces a linear force along its length. However, linear motors are not necessarily straight. Characteristically, a linear motor's active section has ends, whereas more conventional motors are arranged as a continuous loop.
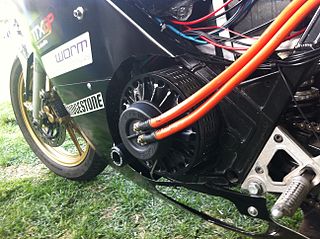
The Lynch motor is a unique axial gap permanent magnet brushed DC electric motor. The motor has a pancake-like shape and was invented by Cedric Lynch in 1979, the relevant patent being filed on 18 December 1986.

Magnet wire or enameled wire is a copper or aluminium wire coated with a very thin layer of insulation. It is used in the construction of transformers, inductors, motors, generators, speakers, hard disk head actuators, electromagnets, electric guitar pickups and other applications that require tight coils of insulated wire.

A monomotor is a train design where a single traction motor powers two or three axles in the same bogie. Conventional bogie design involves either having one motor for each axle, or having one or more axles unpowered. The monomotor design causes the motor to give both axles the same number of revolutions per minute.

A motor capacitor, such as a start capacitor or run capacitor is an electrical capacitor that alters the current to one or more windings of a single-phase alternating-current induction motor to create a rotating magnetic field.

Motor drive, or simply known as drive, describes equipment used to control the speed of machinery. Many industrial processes such as assembly lines must operate at different speeds for different products. Where process conditions demand adjustment of flow from a pump or fan, varying the speed of the drive may save energy compared with other techniques for flow control.

A motor soft starter is a device used with AC electrical motors to temporarily reduce the load and torque in the powertrain and electric current surge of the motor during start-up. This reduces the mechanical stress on the motor and shaft, as well as the electrodynamic stresses on the attached power cables and electrical distribution network, extending the lifespan of the system.

Motor-CAD is an Electromagnetic and Thermal analysis package for electric motors and generators, developed and sold by Motor Design Ltd. It was initially released in 1999.

Froment's "mouse mill" motor was an early form of electric motor, also known as the Revolving Armature Engine. It has similarities to both the synchronous motor and the contemporary stepper motor.

Newman's Energy Machine was a DC motor which the inventor, Joseph Newman, claimed to produce mechanical power exceeding the electrical power being supplied to it. In 1979, Newman attempted to patent the device, but was rejected by the United States Patent Office as being a perpetual motion machine. When the rejection was later appealed, the United States district court requested that Newman's machine be tested by the National Bureau of Standards (NBS). The NBS concluded in June 1986 that output power was not greater than the input. Thus, the patent was again denied. The scientific community has rejected Newman's ideas about electricity and magnetism as pseudoscientific and his claims as false.

Nidec Corporation is a Japanese manufacturer and distributor of electric motors. Their products are found in hard-disk drives, electric appliances, automobiles and commercial and manufacturing equipment. The company has the largest global market share for the tiny spindle motors that power hard-disk drives.

The term outrunner refers to a type of brushless DC electric motor primarily used in electrically propelled, radio-controlled model aircraft.

A permanent magnet motor is a type of electric motor that uses permanent magnets in addition to windings on its field, rather than windings only.
A piezoelectric motor or piezo motor is a type of electric motor based on the change in shape of a piezoelectric material when an electric field is applied, as a consequence of the converse piezoelectric effect. An electrical circuit makes acoustic or ultrasonic vibrations in the piezoelectric material, most often lead zirconate titanate and occasionally lithium niobate or other single-crystal materials, which can produce linear or rotary motion depending on their mechanism. Examples of types piezoelectric motors include inchworm motors, stepper and slip-stick motors as well as ultrasonic motors which can further be further categorized into standing wave and travelling wave motors. Piezoelectric motors typically use a cyclic stepping motion, which allows the oscillation of the crystals to produce an arbitrarily large motion, as opposed to most other piezoelectric actuators where the range of motion is limited by the static strain that may be induced in the piezoelectric element.
A reciprocating electric motor is a motor in which the armature moves back and forth rather than circularly. Early electric motors were sometimes of the reciprocating type, such as those made by Daniel Davis in the 1840s. Today, reciprocating electric motors are rare but they do have some niche applications, e.g. in linear compressors for cryogenics and as educational toys.

A reluctance motor is a type of electric motor that induces non-permanent magnetic poles on the ferromagnetic rotor. The rotor does not have any windings. It generates torque through magnetic reluctance.

A repulsion motor is a type of electric motor which runs on alternating current (AC). It was formerly used as a traction motor for electric trains but has been superseded by other types of motors. Repulsion motors are classified as single phase motors.

The rotor is a moving component of an electromagnetic system in the electric motor, electric generator, or alternator. Its rotation is due to the interaction between the windings and magnetic fields which produces a torque around the rotor's axis.

A Sawyer motor or planar motor is a type of linear electric motor with a forcer capable of moving in two dimensions, riding on a stator which is a large flat—or nearly flat—plate. Sawyer motors have been used in positioning stages and pen plotters.
The universal motor is a type of electric motor that can operate on either AC or DC power and uses an electromagnet as its stator to create its magnetic field. It is a commutated series-wound motor where the stator's field coils are connected in series with the rotor windings through a commutator. It is often referred to as an AC series motor. The universal motor is very similar to a DC series motor in construction, but is modified slightly to allow the motor to operate properly on AC power. This type of electric motor can operate well on AC because the current in both the field coils and the armature will alternate synchronously with the supply. Hence the resulting mechanical force will occur in a consistent direction of rotation, independent of the direction of applied voltage, but determined by the commutator and polarity of the field coils.

A servomotor is a rotary actuator or linear actuator that allows for precise control of angular or linear position, velocity and acceleration. It consists of a suitable motor coupled to a sensor for position feedback. It also requires a relatively sophisticated controller, often a dedicated module designed specifically for use with servomotors.

Shaded-pole synchronous motors are a class of AC motors.

A slip ring is an electromechanical device that allows the transmission of power and electrical signals from a stationary to a rotating structure. A slip ring can be used in any electromechanical system that requires rotation while transmitting power or signals. It can improve mechanical performance, simplify system operation and eliminate damage-prone wires dangling from movable joints.

A split-phase or single-phase three-wire system is a type of single-phase electric power distribution. It is the alternating current (AC) equivalent of the original Edison Machine Works three-wire direct-current system. Its primary advantage is that, for a given capacity of a distribution system, it saves conductor material over a single-ended single-phase system, while only requiring a single phase on the supply side of the distribution transformer.
The stator is the stationary part of a rotary system, found in electric generators, electric motors, sirens, mud motors or biological rotors. Energy flows through a stator to or from the rotating component of the system. In an electric motor, the stator provides a magnetic field that drives the rotating armature; in a generator, the stator converts the rotating magnetic field to electric current. In fluid powered devices, the stator guides the flow of fluid to or from the rotating part of the system.

A stepper motor, also known as step motor or stepping motor, is a brushless DC electric motor that divides a full rotation into a number of equal steps. The motor's position can be commanded to move and hold at one of these steps without any position sensor for feedback, as long as the motor is correctly sized to the application in respect to torque and speed.

In electrical engineering, a synchronous condenser is a DC-excited synchronous motor, whose shaft is not connected to anything but spins freely. Its purpose is not to convert electric power to mechanical power or vice versa, but to adjust conditions on the electric power transmission grid. Its field is controlled by a voltage regulator to either generate or absorb reactive power as needed to adjust the grid's voltage, or to improve power factor. The condenser’s installation and operation are identical to large electric motors and generators.

A synchronous electric motor is an AC motor in which, at steady state, the rotation of the shaft is synchronized with the frequency of the supply current; the rotation period is exactly equal to an integral number of AC cycles. Synchronous motors contain multiphase AC electromagnets on the stator of the motor that create a magnetic field which rotates in time with the oscillations of the line current. The rotor with permanent magnets or electromagnets turns in step with the stator field at the same rate and as a result, provides the second synchronized rotating magnet field of any AC motor. A synchronous motor is termed doubly fed if it is supplied with independently excited multiphase AC electromagnets on both the rotor and stator.

An ultrasonic motor is a type of piezoelectric motor powered by the ultrasonic vibration of a component, the stator, placed against another component, the rotor or slider depending on the scheme of operation. Ultrasonic motors differ from other piezoelectric motors in several ways, though both typically use some form of piezoelectric material, most often lead zirconate titanate and occasionally lithium niobate or other single-crystal materials. The most obvious difference is the use of resonance to amplify the vibration of the stator in contact with the rotor in ultrasonic motors. Ultrasonic motors also offer arbitrarily large rotation or sliding distances, while piezoelectric actuators are limited by the static strain that may be induced in the piezoelectric element.
The universal motor is a type of electric motor that can operate on either AC or DC power and uses an electromagnet as its stator to create its magnetic field. It is a commutated series-wound motor where the stator's field coils are connected in series with the rotor windings through a commutator. It is often referred to as an AC series motor. The universal motor is very similar to a DC series motor in construction, but is modified slightly to allow the motor to operate properly on AC power. This type of electric motor can operate well on AC because the current in both the field coils and the armature will alternate synchronously with the supply. Hence the resulting mechanical force will occur in a consistent direction of rotation, independent of the direction of applied voltage, but determined by the commutator and polarity of the field coils.