Pottery is the process and the products of forming vessels and other objects with clay and other ceramic materials, which are fired at high temperatures to give them a hard, durable form. Major types include earthenware, stoneware and porcelain. The place where such wares are made by a potter is also called a pottery. The definition of pottery, used by the ASTM International, is "all fired ceramic wares that contain clay when formed, except technical, structural, and refractory products." In archaeology, especially of ancient and prehistoric periods, "pottery" often means vessels only, and figures of the same material are called "terracottas." Clay as a part of the materials used is required by some definitions of pottery, but this is dubious.

Art pottery is a term for pottery with artistic aspirations, made in relatively small quantities, mostly between about 1870 and 1930. Typically, sets of the usual tableware items are excluded from the term; instead the objects produced are mostly decorative vessels such as vases, jugs, bowls and the like which are sold singly. The term originated in the later 19th century, and is usually used only for pottery produced from that period onwards. It tends to be used for ceramics produced in factory conditions, but in relatively small quantities, using skilled workers, with at the least close supervision by a designer or some sort of artistic director. Studio pottery is a step up, supposed to be produced in even smaller quantities, with the hands-on participation of an artist-potter, who often performs all or most of the production stages. But the use of both terms can be elastic. Ceramic art is often a much wider term, covering all pottery that comes within the scope of art history, but "ceramic artist" is often used for hands-on artist potters in studio pottery.

Biscuit refers to any pottery that has been fired in a kiln without a ceramic glaze. This can be a final product such as biscuit porcelain or unglazed earthenware or, most commonly, an intermediate stage in a glazed final product.

Black-on-black ware is a 20th- and 21st-century pottery tradition developed by Puebloan Native American ceramic artists in Northern New Mexico. Traditional reduction-fired blackware has been made for centuries by pueblo artists and other artists around the world. Pueblo black-on-black ware of the past century is produced with a smooth surface, with the designs applied through selective burnishing or the application of refractory slip. Another style involves carving or incising designs and selectively polishing the raised areas. For generations several families from Kha'po Owingeh and P'ohwhóge Owingeh pueblos have been making black-on-black ware with the techniques passed down from matriarch potters. Artists from other pueblos have also produced black-on-black ware. Several contemporary artists have created works honoring the pottery of their ancestors.

Bone china is a type of porcelain that is composed of bone ash, feldspathic material, and kaolin. It has been defined as "ware with a translucent body" containing a minimum of 30% of phosphate derived from animal bone and calculated calcium phosphate. Bone china is the strongest of the porcelain or china ceramics, having very high mechanical and physical strength and chip resistance, and is known for its high levels of whiteness and translucency. Its high strength allows it to be produced in thinner cross-sections than other types of porcelain. Like stoneware it is vitrified, but is translucent due to differing mineral properties.

A cavetto is a concave moulding with a regular curved profile that is part of a circle, widely used in architecture as well as furniture, picture frames, metalwork and other decorative arts. In describing vessels and similar shapes in pottery, metalwork and related fields, "cavetto" may be used of a variety of concave curves running round objects. The word comes from Italian, as a diminutive of cave, from the Latin for "hollow". A vernacular alternative is "cove", most often used where interior walls curve at the top to make a transition to the roof, or for "upside down" cavettos at the bases of elements.

Ceramic art is art made from ceramic materials, including clay. It may take forms including artistic pottery, including tableware, tiles, figurines and other sculpture. As one of the plastic arts, ceramic art is one of the visual arts. While some ceramics are considered fine art, as pottery or sculpture, most are considered to be decorative, industrial or applied art objects. Ceramics may also be considered artefacts in archaeology. Ceramic art can be made by one person or by a group of people. In a pottery or ceramic factory, a group of people design, manufacture and decorate the art ware. Products from a pottery are sometimes referred to as "art pottery". In a one-person pottery studio, ceramists or potters produce studio pottery.

Ceramic glaze is an impervious layer or coating of a vitreous substance which has been fused to a pottery body through firing. Glaze can serve to color, decorate or waterproof an item. Glazing renders earthenware vessels suitable for holding liquids, sealing the inherent porosity of unglazed biscuit earthenware. It also gives a tougher surface. Glaze is also used on stoneware and porcelain. In addition to their functionality, glazes can form a variety of surface finishes, including degrees of glossy or matte finish and color. Glazes may also enhance the underlying design or texture either unmodified or inscribed, carved or painted.
A ceramics museum is a museum wholly or largely devoted to ceramics, usually ceramic art. Its collections may also include glass and enamel, but typically concentrate on pottery, including porcelain. Most national collections are in a more general museum covering all of the arts, or just the decorative arts. However, there are a number of specialized ceramics museums, with some focusing on the ceramics of just one country, region or manufacturer. Others have international collections, which may be centered on ceramics from Europe or East Asia or have a more global emphasis.

Native American pottery is an art form with at least a 7500-year history in the Americas. Pottery is fired ceramics with clay as a component. Ceramics are used for utilitarian cooking vessels, serving and storage vessels, pipes, funerary urns, censers, musical instruments, ceremonial items, masks, toys, sculptures, and a myriad of other art forms.
Coiling is a method of creating pottery. It has been used to shape clay into vessels for many thousands of years. It is found across the cultures of the world, including Africa, Greece, China, and Native American cultures of New Mexico. Using the coiling technique, it is possible to build thicker or taller walled vessels, which may not have been possible using earlier methods. The technique permits control of the walls as they are built up and allows building on top of the walls to make the vessel look bigger and bulge outward or narrow inward with less danger of collapsing. To do this, the potter takes a pliable material then rolls it until it forms a coil, or long pliable cylinder. By placing one coil on top of another, different shapes can be formed. As this is done while the clay is still fresh and soft, individual coils can be joined seamlessly with simple pressure, rather than by scoring and/or applying slip to the surface. Optionally, coils may only be joined internally or externally, leaving them visible on the other side as an aesthetic choice.

Craquelure is a fine pattern of dense cracking formed on the surface of materials. It can be a result of drying, aging, intentional patterning, or a combination of all three. The term is most often used to refer to tempera or oil paintings, but it can also develop in old ivory carvings or painted miniatures on an ivory backing. Recently, analysis of craquelure has been proposed as a way to authenticate art.
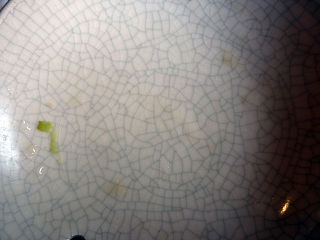
Crazing is the phenomenon that produces a network of fine cracks on the surface of a material, for example in a glaze layer. Crazing frequently precedes fracture in some glassy thermoplastic polymers. As it only takes place under tensile stress, the plane of the crazing corresponds to the stress direction. The effect is visibly distinguishable from other types of fine cracking because the crazing region has different refractive indices from surrounding material. Crazing occurs in regions of high hydrostatic tension, or in regions of very localized yielding, which leads to the formation of interpenetrating microvoids and small fibrils. If an applied tensile load is sufficient, these bridges elongate and break, causing the microvoids to grow and coalesce; as microvoids coalesce, cracks begin to form.

A cup is an close-top container used to hold or cold liquids for pouring or drinking; while mainly used for drinking, it also can be used to store solids for pouring. Cups may be made of glass, metal, china, clay, wood, stone, polystyrene, plastic, aluminium or other materials, and are usually fixed with a stem, handles, or other adornments. Cups are used for quenching thirst across a wide range of cultures and social classes, and different styles of cups may be used for different liquids or in different situations. Cups of different styles may be used for different types of liquids or other foodstuffs, in different situations ,or for decoration.
Earthenware is glazed or unglazed nonvitreous pottery that has normally been fired below 1,200 °C (2,190 °F). Basic earthenware, often called terracotta, absorbs liquids such as water. However, earthenware can be made impervious to liquids by coating it with a ceramic glaze, which the great majority of modern domestic earthenware has. The main other important types of pottery are porcelain, bone china, and stoneware, all fired at high enough temperatures to vitrify.

Egyptian faience is a sintered-quartz ceramic material from Ancient Egypt. The sintering process "covered [the material] with a true vitreous coating" as the quartz underwent vitrification, creating a bright lustre of various colours "usually in a transparent blue or green isotropic glass". Its name in the Ancient Egyptian language was tjehenet, and modern archeological terms for it include sintered quartz, glazed frit, and glazed composition. Tjehenet is distinct from the crystalline pigment Egyptian blue, for which it has sometimes incorrectly been used as a synonym.

Faience or faïence is the general English language term for fine tin-glazed pottery.

Fritware, also known as stone-paste, is a type of pottery in which frit is added to clay to reduce its fusion temperature. The mixture may include quartz or other siliceous material. An organic compound such as gum or glue may be added for binding. The resulting mixture can be fired at a lower temperature than clay alone. A glaze is then applied on the surface to harden the object.

Glaze defects are any flaws in the surface quality of a ceramic glaze, its physical structure or its interaction with the body.

Medieval Islamic pottery occupied a geographical position between Chinese ceramics, the unchallenged leaders of Eurasian production, and the pottery of the Byzantine Empire and Europe. For most of the period it can fairly be said to have been between the two in terms of aesthetic achievement and influence as well, borrowing from China and exporting to and influencing Byzantium and Europe. The use of drinking and eating vessels in gold and silver, the ideal in ancient Rome and Persia as well as medieval Christian societies, is prohibited by the Hadiths, with the result that pottery and glass were used for tableware by Muslim elites, as pottery also was in China but was much rarer in Europe and Byzantium. In the same way, Islamic restrictions greatly discouraged figurative wall-painting, encouraging the architectural use of schemes of decorative and often geometrically-patterned titles, which are the most distinctive and original specialty of Islamic ceramics.

Iznik pottery, or Iznik ware, named after the town of İznik in western Anatolia where it was made, is a decorated ceramic that was produced from the last quarter of the 15th century until the end of the 17th century.
A kiln is a thermally insulated chamber, a type of oven, that produces temperatures sufficient to complete some process, such as hardening, drying, or chemical changes. Kilns have been used for millennia to turn objects made from clay into pottery, tiles and bricks. Various industries use rotary kilns for pyroprocessing—to calcinate ores, to calcinate limestone to lime for cement, and to transform many other materials.

Lead-glazed earthenware is one of the traditional types of earthenware with a ceramic glaze, which coats the ceramic biscuit body and renders it impervious to liquids, as terracotta itself is not. Plain lead glaze is shiny and transparent after firing. Coloured lead glazes are shiny and either translucent or opaque after firing. Three other traditional techniques are tin-glazed, which coats the ware with an opaque white glaze suited for overglaze brush-painted colored enamel designs; salt glaze pottery, also often stoneware; and the feldspathic glazes of Asian porcelain. Modern materials technology has invented new vitreous glazes that do not fall into these traditional categories.
In pottery, leather-hard is the condition of a clay or clay body when it has been partially dried to the point where all shrinkage has been completed, and it has a consistency similar to leather of the same thickness as the clay. At this stage, the clay object has approximately 15% moisture content. The clay is still visibly damp but has dried enough to be able to be handled without deformation. The body is able to be gouged or incised without breaking.
A lug is a typically flattened protuberance, a handle or extrusion located on the side of a ceramics, jug, glass, vase, or other container. They are sometimes found on prehistoric ceramics and stone containers, such as on pots from ancient Egypt, Hembury ware, claw beakers, and boar spears.

In different periods of time and in different countries the word majolica has been used for two distinct types of pottery.

A muffle furnace or muffle oven is a furnace in which the subject material is isolated from the fuel and all of the products of combustion, including gases and flying ash. After the development of high-temperature heating elements and widespread electrification in developed countries, new muffle furnaces quickly moved to electric designs.

Palissy ware is a 19th-century term for ceramics produced in the style of the famous French potter Bernard Palissy, who referred to his own work in the familiar manner as rustique. It is therefore also known as rusticware. Palissy's distinctive style of polychrome lead-glazed earthenware in a sombre earth-toned palette, using naturalistic scenes of plants and animals cast from life, was much imitated by other potters both in his own lifetime and especially in the 19th century. In this revival, pottery in Palissy's style was produced by Charles-Jean Avisseau of Tours, who rediscovered Palissy's techniques in 1843, his relatives the Landais family of Tours, Georges Pull of Paris, Maurice, and Barbizet.
A pinch pot is a simple form of hand-made pottery produced from ancient times to the present. The pinching method is to create pottery that can be ornamental or functional, and has been widely employed across culture. The method used is to simply have a lob of clay, then pinch it to the shape desired.

Pit firing is the oldest known method for the firing of pottery. Examples have been dated as early as 29,000–25,000 BCE, while the earliest known kiln dates to around 6000 BCE, and was found at the Yarim Tepe site in modern Iraq. Kilns allow higher temperatures to be reached, and use fuel more efficiently, and have long replaced pit firing as the most widespread method of firing pottery, although the technique still finds limited use amongst certain studio potters and in Africa.

Porcelain is a ceramic material made by heating substances, generally including a material like kaolin, in a kiln to temperatures between 1,200 and 1,400 °C. The strength, and translucence of porcelain, relative to other types of pottery, arises mainly from vitrification and the formation of the mineral mullite within the body at these high temperatures. Though definitions vary, porcelain can be divided into three main categories: hard-paste, soft-paste and bone china. The category that an object belongs to depends on the composition of the paste used to make the body of the porcelain object and the firing conditions.

In pottery, a potter's wheel is a machine used in the shaping of round ceramic ware. The wheel may also be used during the process of trimming the excess body from dried ware, and for applying incised decoration or rings of colour. Use of the potter's wheel became widespread throughout the Old World but was unknown in the Pre-Columbian New World, where pottery was handmade by methods that included coiling and beating.
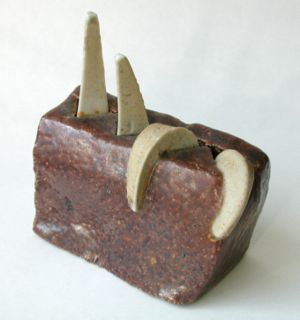
Pyrometric cones are pyrometric devices that are used to gauge heatwork during the firing of ceramic materials. The cones, often used in sets of three, are positioned in a kiln with the wares to be fired and provide a visual indication of when the wares have reached a required state of maturity, a combination of time and temperature. Thus, pyrometric cones give a temperature equivalent; they are not simple temperature-measuring devices.

A resist, used in many areas of manufacturing and art, is something that is added to parts of an object to create a pattern by protecting these parts from being affected by a subsequent stage in the process. Often the resist is then removed.

Restaurant ware, or most commonly hotelware is vitrified, ceramic tableware which exhibits high mechanical strength and is produced for use in hotels and restaurants. Tableware used in railway dining cars, passenger ships and airlines are also included in this category.

A saggar is a type of kiln furniture. It is a ceramic boxlike container used in the firing of pottery to enclose or protect ware being fired inside a kiln. Traditionally, saggars were made primarily from fireclay. Saggars have been used to protect, or safeguard, ware from open flame, smoke, gases and kiln debris: the name may be a contraction of the word safeguard. Their use is widespread, including in China, Korea, Japan and the United Kingdom. Saggars are still used in the production of ceramics to shield ware from the direct contact of flames and from damage by kiln debris. Modern saggars are made of alumina ceramic, cordierite ceramic, mullite ceramic silicon carbide and in special cases from zirconia.
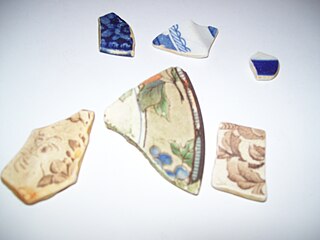
Sea pottery is pottery which is broken into worn pieces and shards and found on beaches along oceans or large lakes. Sea pottery has been tumbled and smoothed by the water and sand, creating small pieces of smooth, frosted pottery. It is often collected with more common sea glass by beachcombers.

A slip is a clay slurry used to produce pottery and other ceramic wares. Liquified clay, in which there is no fixed ratio of water and clay, is called slip or clay slurry which is used either for joining leather-hard (semi-hardened) clay body together by slipcasting with mould, glazing or decorating the pottery by paining or dipping the pottery with slip. Pottery on which slip has been applied either for glazing or decoration is called the slipware.
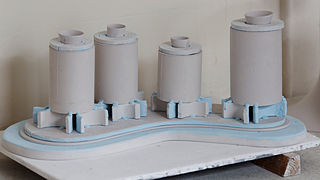
Slip casting, or slipcasting, is a ceramic forming technique for pottery and other ceramics, especially for shapes not easily made on a wheel. In this method, a liquid clay body slip is poured into plaster moulds and allowed to form a layer, the cast, on the inside walls of the mould. The process usually takes at least 24 hours per piece. It gives very precise and consistent shapes, and is now the most common technique used for commercial mass-produced pottery, although it began as a technique for fine pottery such as European porcelain in the 1750s, and Chinese Jingdezhen porcelain considerably earlier.

Soft-paste porcelain is a type of ceramic material in pottery, usually accepted as a type of porcelain. It is weaker than "true" hard-paste porcelain, and does not require either the high firing temperatures or the special mineral ingredients needed for that. There are many types, using a range of materials. The material originated in the attempts by many European potters to replicate hard-paste Chinese export porcelain, especially in the 18th century, and the best versions match hard-paste in whiteness and translucency, but not in strength. But the look and feel of the material can be highly attractive, and it can take painted decoration very well.
Stilts are small supports used when firing glazed ceramics to stop the melting glaze from fusing them to each other or the kiln. Stilts are a form of kiln furniture. Their presence in archaeological sites along with other kiln furniture such as saggars and kiln bars can be used to support a case for local production. Some potters avoid the need for stilts by not glazing the bottom of their products. This is known as dry footing.

Stoneware is a rather broad term for pottery or other ceramics fired at a relatively high temperature. A modern technical definition is a vitreous or semi-vitreous ceramic made primarily from stoneware clay or non-refractory fire clay. Whether vitrified or not, it is nonporous ; it may or may not be glazed. Historically, across the world, it has been developed after earthenware and before porcelain, and has often been used for high-quality as well as utilitarian wares.

Studio pottery is pottery made by professional and amateur artists or artisans working alone or in small groups, making unique items or short runs. Typically, all stages of manufacture are carried out by the artists themselves. Studio pottery includes functional wares such as tableware and cookware, and non-functional wares such as sculpture, with vases and bowls covering the middle ground, often being used only for display. Studio potters can be referred to as ceramic artists, ceramists, ceramicists or as an artist who uses clay as a medium.

Tableware is any dish or dishware used for setting a table, serving food, and dining. It includes cutlery, glassware, serving dishes, and other items for practical as well as decorative purposes. The quality, nature, variety and number of objects varies according to culture, religion, number of diners, cuisine and occasion. For example, Middle Eastern, Indian or Polynesian food culture and cuisine sometimes limits tableware to serving dishes, using bread or leaves as individual plates. Special occasions are usually reflected in higher quality tableware.

Terracotta, terra cotta, or terra-cotta, a type of earthenware, is a clay-based unglazed or glazed ceramic, where the fired body is porous. Terracotta is the term normally used for sculpture made in earthenware, and also for various practical uses including vessels, water and waste water pipes, roofing tiles, bricks, and surface embellishment in building construction. The term is also used to refer to the natural brownish orange color of most terracotta.

Tin-glazed pottery is earthenware covered in lead glaze with added tin oxide which is white, shiny and opaque ; usually this provides a background for brightly painted decoration. It has been important in Islamic and European pottery, but very little used in East Asia. The pottery body is usually made of red or buff-colored earthenware and the white glaze imitated Chinese porcelain. The decoration on tin-glazed pottery is usually applied to the unfired glaze surface by brush with metallic oxides, commonly cobalt oxide, copper oxide, iron oxide, manganese dioxide and antimony oxide. The makers of Italian tin-glazed pottery from the late Renaissance blended oxides to produce detailed and realistic polychrome paintings.

A Toby Jug, also sometimes known as a Fillpot, is a pottery jug in the form of a seated person, or the head of a recognizable person. Typically the seated figure is a heavy-set, jovial man holding a mug of beer in one hand and a pipe of tobacco in the other and wearing 18th-century attire: a long coat and a tricorn hat. The tricorn hat forms a pouring spout, often with a removable lid, and a handle is attached at the rear. Jugs depicting just the head and shoulders of a figure are also referred to as Toby jugs, although these should strictly be called "character jugs" or face jugs, the wider historical term.

Victorian majolica properly refers to two types of majolica made in the second half of the 19th century in Europe and America.
Vitreous enamel, also called porcelain enamel, is a material made by fusing powdered glass to a substrate by firing, usually between 750 and 850 °C. The powder melts, flows, and then hardens to a smooth, durable vitreous coating. The word comes from the Latin vitreum, meaning "glass".

Zellīj is a style of mosaic tilework made from individually hand-chiseled tile pieces set into a plaster base. The pieces were typically of different colours and fitted together to form elaborate geometric motifs, such as radiating star patterns. This form of Islamic art is one of the main characteristics of Moroccan architecture and medieval Moorish architecture. Zellij became a standard decorative element along lower walls, in fountains and pools, and for the paving of floors. It is found commonly in historic buildings throughout the region, as well as in modern buildings making use of traditional designs such as the Hassan II Mosque in Casablanca which adds a new color palette with traditional designs.
