
A gear is a rotating circular machine part having cut teeth or, in the case of a cogwheel or gearwheel, inserted teeth, which mesh with another (compatible) toothed part to transmit (convert) torque and speed. The basic principle behind the operation of gears is analogous to the basic principle of levers. A gear may also be known informally as a cog. Geared devices can change the speed, torque, and direction of a power source. Gears of different sizes produce a change in torque, creating a mechanical advantage, through their gear ratio, and thus may be considered a simple machine. The rotational speeds, and the torques, of two meshing gears differ in proportion to their diameters. The teeth on the two meshing gears all have the same shape.

The American Gear Manufacturers Association (AGMA) is a voluntary association of companies, consultants, and academicians with a direct interest in the design, manufacture, and application of gears, couplings and related power transmission components and equipment.

In mechanical engineering, backlash, sometimes called lash, play, or slop, is a clearance or lost motion in a mechanism caused by gaps between the parts. It can be defined as "the maximum distance or angle through which any part of a mechanical system may be moved in one direction without applying appreciable force or motion to the next part in mechanical sequence."p. 1-8 An example, in the context of gears and gear trains, is the amount of clearance between mated gear teeth. It can be seen when the direction of movement is reversed and the slack or lost motion is taken up before the reversal of motion is complete. It can be heard from the railway couplings when a train reverses direction. Another example is in a valve train with mechanical tappets, where a certain range of lash is necessary for the valves to work properly.

Bevel gears are gears where the axes of the two shafts intersect and the tooth-bearing faces of the gears themselves are conically shaped. Bevel gears are most often mounted on shafts that are 90 degrees apart, but can be designed to work at other angles as well. The pitch surface of bevel gears is a cone.

A crown gear is a gear which has teeth that project at right angles to the face of the wheel. In particular, a crown gear is a type of bevel gear where the pitch cone angle is 90 degrees. A pitch cone of any other angle is simply called a bevel gear. Crown gears normally mesh with other bevel gears, or sometimes spur gears, a typical use being a crown gear and pinion system which allows a rotary motion to be shifted 90 degrees.

The cycloidal gear profile is a form of toothed gear used in mechanical clocks, rather than the involute gear form used for most other gears. The gear tooth profile is based on the epicycloid and hypocycloid curves, which are the curves generated by a circle rolling around the outside and inside of another circle, respectively.

A cycloidal drive or cycloidal speed reducer is a mechanism for reducing the speed of an input shaft by a certain ratio. Cycloidal speed reducers are capable of relatively high ratios in compact sizes with very low backlash.

A differential is a gear train with three shafts that has the property that the rotational speed of one shaft is the average of the speeds of the others, or a fixed multiple of that average.
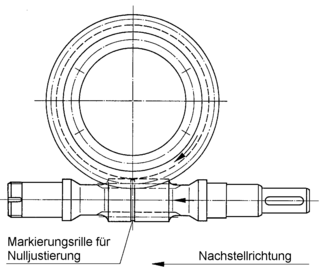
A duplex worm or dual lead worm is a worm gear set where the two flanks are manufactured with slightly different modules and/or diameter quotients. As a result of this, different lead angles on both tooth profiles are obtained, so that the tooth thickness is continuously increasing all over the worm length, while the gap between two threads is decreasing. This allows control of backlash.

An epicyclic gear train consists of two gears mounted so that the center of one gear revolves around the center of the other. A carrier connects the centers of the two gears and rotates to carry one gear, called the planet gear or planet pinion, around the other, called the sun gear or sun wheel. The planet and sun gears mesh so that their pitch circles roll without slip. A point on the pitch circle of the planet gear traces an epicycloid curve. In this simplified case, the sun gear is fixed and the planetary gear(s) roll around the sun gear.

A gear bearing is a type of rolling-element bearing similar to an epicyclic gear. Gear bearings consist of a number of smaller 'satellite' gears which revolve around the center of the bearing along a track on the outsides of the internal and satellite gears, and on the inside of the external gear. Each gear is in between two concentric rings. Therefore, the widths of the satellite gears must all be the same.

Gear oil is a lubricant made specifically for transmissions, transfer cases, and differentials in automobiles, trucks, and other machinery. It is of a high viscosity and usually contains organosulfur compounds. Some modern automatic transaxles do not use a heavy oil at all but lubricate with the lower viscosity hydraulic fluid, which is available at pressure within the automatic transmission. Gear oils account for about 20% of the lubricant market.

Gear shaping is a machining process for creating teeth on a gear using a cutter. Gear shaping is a convenient and versatile method of gear cutting. It involves continuous, same-plane rotational cutting of gear.

A gear train is a mechanical system formed by mounting gears on a frame so the teeth of the gears engage.

The Geneva drive or Maltese cross is a gear mechanism that translates a continuous rotation movement into intermittent rotary motion.

In mechanical engineering, a helix angle is the angle between any helix and an axial line on its right, circular cylinder or cone. Common applications are screws, helical gears, and worm gears.

A herringbone gear, a specific type of double helical gear, is a special type of gear that is a side-to-side combination of two helical gears of opposite hands. From the top, each helical groove of this gear looks like the letter V, and many together form a herringbone pattern. Unlike helical gears, herringbone gears do not produce an additional axial load.

Hobbing is a machining process for gear cutting, cutting splines, and cutting sprockets on a hobbing machine, which is a special type of milling machine. The teeth or splines of the gear are progressively cut into the material by a series of cuts made by a cutting tool called a hob. Compared to other gear forming processes it is relatively inexpensive but still quite accurate, thus it is used for a broad range of parts and quantities.

The involute gear profile is the most commonly used system for gearing today, with cycloid gearing still used for some specialties such as clocks. In an involute gear, the profiles of the teeth are involutes of a circle. The involute of a circle is the spiraling curve traced by the end of an imaginary taut string unwinding itself from that stationary circle called the base circle, or (equivalently) a triangle wave projected on the circumference of a circle.

A layshaft is an intermediate shaft within a gearbox that carries gears, but does not transfer the primary drive of the gearbox either in or out of the gearbox. Layshafts are best known through their use in car gearboxes, where they were a ubiquitous part of the rear-wheel drive layout. With the shift to front-wheel drive, the use of layshafts is now rarer.
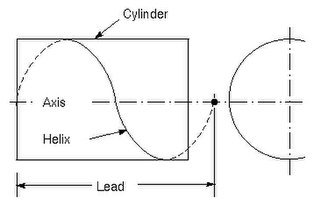
Lead is the axial advance of a helix or screw during one complete turn (360°) The lead for a screw thread is the axial travel for a single revolution.
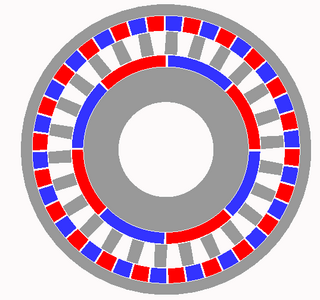
A magnetic gear resembles the traditional mechanical gear in geometry and function, using magnets instead of teeth. As two opposing magnets approach each other, they repel; when placed on two rings the magnets will act like teeth. As opposed to conventional hard contact backlash in a spur gear, where a gear may rotate freely until in contact with the next gear, the magnetic gear has a springy backlash. As a result magnetic gears are able to apply pressure no matter the relative angle. Although they provide a motion ratio as a traditional gear, such gears work without touching and are immune to wear of mating surfaces, have no noise, and may slip without damage.
A non-circular gear (NCG) is a special gear design with special characteristics and purpose. While a regular gear is optimized to transmit torque to another engaged member with minimum noise and wear and with maximum efficiency, a non-circular gear's main objective might be ratio variations, axle displacement oscillations and more. Common applications include textile machines, potentiometers, CVTs, window shade panel drives, mechanical presses and high torque hydraulic engines.

A non-synchronous transmission, also called a crash gearbox, is a form of manual transmission based on gears that do not use synchronizing mechanisms. They require the driver to manually synchronize the transmission's input speed and output speed.

A pinion is a round gear—usually the smaller of two meshed gears—used in several applications, including drivetrain and rack and pinion systems.

Pressure angle in relation to gear teeth, also known as the angle of obliquity, is the angle between the tooth face and the gear wheel tangent. It is more precisely the angle at a pitch point between the line of pressure and the plane tangent to the pitch surface. The pressure angle gives the direction normal to the tooth profile. The pressure angle is equal to the profile angle at the standard pitch circle and can be termed the "standard" pressure angle at that point. Standard values are 14.5 and 20 degrees. Earlier gears with pressure angle 14.5 were commonly used because the cosine is larger for a smaller angle, providing more power transmission and less pressure on the bearing; however, teeth with smaller pressure angles are weaker. To run gears together properly their pressure angles must be matched.

A gear is a rotating circular machine part having cut teeth or, in the case of a cogwheel or gearwheel, inserted teeth, which mesh with another (compatible) toothed part to transmit (convert) torque and speed. The basic principle behind the operation of gears is analogous to the basic principle of levers. A gear may also be known informally as a cog. Geared devices can change the speed, torque, and direction of a power source. Gears of different sizes produce a change in torque, creating a mechanical advantage, through their gear ratio, and thus may be considered a simple machine. The rotational speeds, and the torques, of two meshing gears differ in proportion to their diameters. The teeth on the two meshing gears all have the same shape.

The profile angle of a gear is the angle at a specified pitch point between a line tangent to a tooth surface and the line normal to the pitch surface. This definition is applicable to every type of gear for which a pitch surface can be defined. The profile angle gives the direction of the tangent to a tooth profile.

A rack and pinion is a type of linear actuator that comprises a circular gear engaging a linear gear, which operate to translate rotational motion into linear motion. Driving the pinion into rotation causes the rack to be driven linearly. Driving the rack linearly will cause the pinion to be driven into a rotation. A rack and pinion drive can use both straight and helical gears. Though some suggest Helical gears are noted for “quieter” operation, there is no science to support this theory. Helical racks while being more affordable, have proven to increase side torque on the datums, increasing operating temperature leading to premature wear. Straight racks require a lower driving force and offer increased torque and speed per percentage of gear ratio which allows lower operating temperature and lessens viscal friction and energy use. The maximum force that can be transmitted in a rack and pinion mechanism is determined by the tooth pitch and the size of the pinion as well as the gear ratio..

The Ravigneaux gearset is a double planetary gear set, invented by Pol Ravigneaux, who filed a patent application on July 28, 1949, in Neuilly-sur-Seine France. This planetary gear set, commonly used in automatic transmissions, is constructed from two gear pairs, ring–planet and planet–planet.

A gear is a rotating circular machine part having cut teeth or, in the case of a cogwheel or gearwheel, inserted teeth, which mesh with another (compatible) toothed part to transmit (convert) torque and speed. The basic principle behind the operation of gears is analogous to the basic principle of levers. A gear may also be known informally as a cog. Geared devices can change the speed, torque, and direction of a power source. Gears of different sizes produce a change in torque, creating a mechanical advantage, through their gear ratio, and thus may be considered a simple machine. The rotational speeds, and the torques, of two meshing gears differ in proportion to their diameters. The teeth on the two meshing gears all have the same shape.

A spiral bevel gear is a bevel gear with helical teeth. The main application of this is in a vehicle differential, where the direction of drive from the drive shaft must be turned 90 degrees to drive the wheels. The helical design produces less vibration and noise than conventional straight-cut or spur-cut gear with straight teeth.

A sprocket, sprocket-wheel or chainwheel is a profiled wheel with teeth that mesh with a chain, track or other perforated or indented material. The name 'sprocket' applies generally to any wheel upon which radial projections engage a chain passing over it. It is distinguished from a gear in that sprockets are never meshed together directly, and differs from a pulley in that sprockets have teeth and pulleys are smooth except for timing pulleys used with toothed belts.

Spur gears or straight-cut gears are the simplest type of gear. They consist of a cylinder or disk with teeth projecting radially. Viewing the gear at 90 degrees from the shaft length the tooth faces are straight and aligned parallel to the axis of rotation. Looking down the length of the shaft, a tooth's cross section is usually not triangular. Instead of being straight the sides of the cross section have a curved form to achieve a constant drive ratio. Spur gears gears mesh together correctly only if fitted to parallel shafts. No axial thrust is created by the tooth loads. Spur gears are excellent at moderate speeds but tend to be noisy at high speeds.
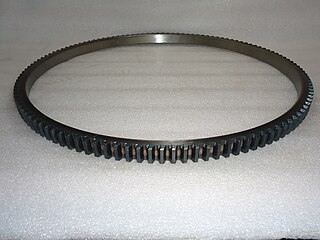
A starter ring gear is a part attached to an internal combustion engine that is part of the assembly which transfers the torque from the starter motor to the engine's crankshaft, in order to start the engine. The starter ring gear is usually made from medium carbon steel.

Strain wave gearing is a type of mechanical gear system that uses a flexible spline with external teeth, which is deformed by a rotating elliptical plug to engage with the internal gear teeth of an outer spline.

A sub transmission is an extra manual or automatic transmission that is independent of the main transmission. In a four-wheel drive, an extra gear stick is often provided to transfer torque when needed and to put the vehicle into low range. Sub transmissions are used in a few motorcycles, such as the Honda CB900C and the Honda CT110. In the Mitsubishi Cordia, a "Super Shift 4x2" sub transmission was adopted, doubling the number of 4-speed main transmission gears.

The sun and planet gear is a method of converting reciprocating motion to rotary motion and was used in the first rotative beam engines.

A torque multiplier is a tool used to provide a mechanical advantage in applying torque to turn bolts, nuts or other items designed to be actuated by application of torque, such as the actuation of valves, particularly where there are relatively high torque requirements.

A worm drive is a gear arrangement in which a worm meshes with a worm wheel. The two elements are also called the worm screw and worm gear. The terminology is often confused by imprecise use of the term worm gear to refer to the worm, the worm wheel, or the worm drive as a unit.
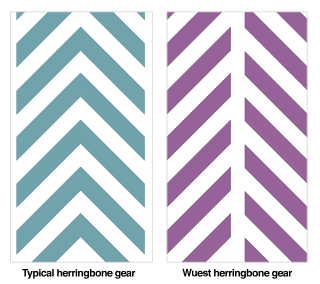
A Wuest type herringbone gear is a special type of herringbone gear wherein "the teeth on opposite sides of the center line are staggered by an amount equal to one half the circular pitch". By having the teeth of two sides staggered, the gear wears more evenly at the slight cost of strength.