
A bearing is a machine element that constrains relative motion to only the desired motion, and reduces friction between moving parts. The design of the bearing may, for example, provide for free linear movement of the moving part or for free rotation around a fixed axis; or, it may prevent a motion by controlling the vectors of normal forces that bear on the moving parts. Most bearings facilitate the desired motion by minimizing friction. Bearings are classified broadly according to the type of operation, the motions allowed, or to the directions of the loads (forces) applied to the parts.

Aerospace bearings are the bearings installed in aircraft and aerospace systems including commercial, private, military, or space applications.

Air bearings are fluid bearings that use a thin film of pressurized gas to provide a low friction load-bearing interface between surfaces. The two surfaces do not touch, thus avoiding the traditional bearing-related problems of friction, wear, particulates, and lubricant handling, and offer distinct advantages in precision positioning, such as lacking backlash and static friction, as well as in high-speed applications. Space craft simulators now most often use air bearings and 3-D printers are now used to make air-bearing-based attitude simulators for CubeSat satellites.
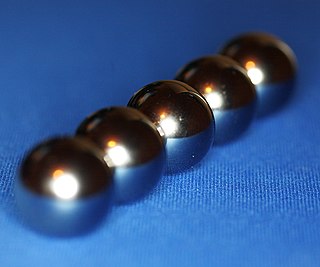
Bearing balls are special highly spherical and smooth balls, most commonly used in ball bearings, but also used as components in things like freewheel mechanisms. The balls come in many different grades. These grades are defined by bodies such as the American Bearing Manufacturers Association (ABMA), a body which sets standards for the precision of bearing balls. They are manufactured in machines designed specially for the job.

In an automobile, ball joints are spherical bearings that connect the control arms to the steering knuckles, and are used on virtually every automobile made. They bionically resemble the ball-and-socket joints found in most tetrapod animals.

A bridge bearing is a component of a bridge which typically provides a resting surface between bridge piers and the bridge deck. The purpose of a bearing is to allow controlled movement and thereby reduce the stresses involved. Possible causes of movement are thermal expansion and contraction, creep, shrinkage, or fatigue due to the properties of the material used for the bearing. External sources of movement include the settlement of the ground below, thermal expansion, and seismic activity. There are several different types of bridge bearings which are used depending on a number of different factors including the bridge span, loading conditions, and performance specifications. The oldest form of bridge bearing is simply two plates resting on top of each other. A common form of modern bridge bearing is the elastomeric bridge bearing. Another type of bridge bearing is the mechanical bridge bearing. There are several types of mechanical bridge bearing, such as the pinned bearing, which in turn includes specific types such as the rocker bearing, and the roller bearing. Another type of mechanical bearing is the fixed bearing, which allows rotation, but not other forms of movement.
Contact mechanics is the study of the deformation of solids that touch each other at one or more points. A central distinction in contact mechanics is between stresses acting perpendicular to the contacting bodies' surfaces and frictional stresses acting tangentially between the surfaces. This page focuses mainly on the normal direction, i.e. on frictionless contact mechanics. Frictional contact mechanics is discussed separately. Normal stresses are caused by applied forces and by the adhesion present on surfaces in close contact even if they are clean and dry.
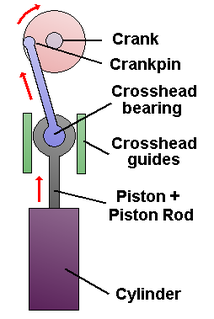
A crosshead is a mechanism used as part of the slider-crank linkages of long reciprocating engines and reciprocating compressors to eliminate sideways pressure on the piston. Also, the crosshead enables the connecting rod to freely move outside the cylinder. Because of the very small bore-to-stroke ratio on such engines, the connecting rod would hit the cylinder walls and block the engine from rotating if the piston was attached directly to the connecting rod like on trunk engines. Therefore, the longitudinal dimension of the crosshead must be matched to the stroke of the engine.

An elastomeric bridge bearing is a commonly used modern bridge bearing. There are several different similar types of bridge bearings that include neoprene bearing pads, neoprene bridge bearings, laminated elastomeric bearings and seismic isolators, which are all generally referred to as bridge bearing pads in the construction industry.

False brinelling is a bearing damage caused by fretting, with or without corrosion, that causes imprints that look similar to brinelling, but are caused by a different mechanism. False brinelling may occur in bearings which act under small oscillations or vibrations.

A flexure bearing is a category of flexure which is engineered to be compliant in one or more angular degrees of freedom. Flexure bearings are often part of compliant mechanisms. Flexure bearings serve much of the same function as conventional bearings or hinges in applications which require angular compliance. However, flexures require no lubrication and exhibit very low or no friction.
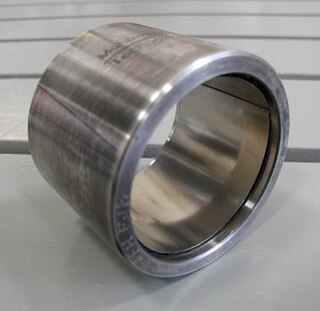
A foil bearing, also known as a foil-air bearing, is a type of air bearing. A shaft is supported by a compliant, spring-loaded foil journal lining. Once the shaft is spinning fast enough, the working fluid pushes the foil away from the shaft so that no contact occurs. The shaft and foil are separated by the air's high pressure, which is generated by the rotation that pulls gas into the bearing via viscosity effects. The high speed of the shaft with respect to the foil is required to initiate the air gap, and once this has been achieved, no wear occurs. Unlike aerostatic or hydrostatic bearings, foil bearings require no external pressurisation system for the working fluid, so the hydrodynamic bearing is self-starting.
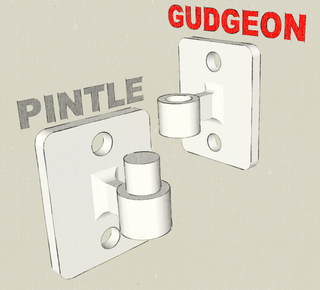
A gudgeon is a socket-like, cylindrical fitting attached to one component to enable a pivoting or hinging connection to a second component. The second component carries a pintle fitting, the male counterpart to the gudgeon, enabling an interpivoting connection that can be easily separated. Designs that may use gudgeon and pintle connections include hinges, shutters and boat rudders.
Contact mechanics is the study of the deformation of solids that touch each other at one or more points. A central distinction in contact mechanics is between stresses acting perpendicular to the contacting bodies' surfaces and frictional stresses acting tangentially between the surfaces. This page focuses mainly on the normal direction, i.e. on frictionless contact mechanics. Frictional contact mechanics is discussed separately. Normal stresses are caused by applied forces and by the adhesion present on surfaces in close contact even if they are clean and dry.

A jewel bearing is a plain bearing in which a metal spindle turns in a jewel-lined pivot hole. The hole is typically shaped like a torus and is slightly larger than the shaft diameter. The jewels are typically made from the mineral corundum, usually either synthetic sapphire or synthetic ruby. Jewel bearings are used in precision instruments where low friction, long life, and dimensional accuracy are important. Their largest use is in mechanical watches.

A magnetic bearing is a type of bearing that supports a load using magnetic levitation. Magnetic bearings support moving parts without physical contact. For instance, they are able to levitate a rotating shaft and permit relative motion with very low friction and no mechanical wear. Magnetic bearings support the highest speeds of any kind of bearing and have no maximum relative speed.

In a piston engine, the main bearings are the bearings which hold the crankshaft in place and allow it to rotate within the engine block.
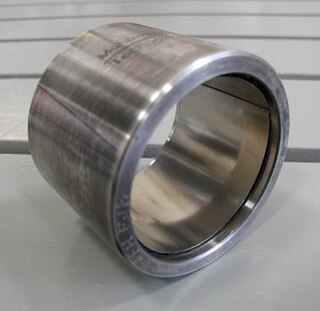
Mohawk Innovative Technology, Inc. is an American product and research and development technology company that develops oil-free foil bearings, magnetic bearings and non-contacting foil seals for high-speed rotating machinery, such as gas turbine engines, turbochargers, compressors, cryogenic pumps, variable high-speed motors/generators and machines.

A pillow block bearing is a pedestal used to provide support for a rotating shaft with the help of compatible bearings & various accessories. The assembly consists of a mounting block which houses a bearing. The block is mounted to a foundation and a shaft is inserted allowing the inner part of the bearing / shaft to rotate. The inside of the bearing is typically 0.001 inches (0.025 mm) larger than the shaft to ensure a tight fit. Set screws, locking collars, or set collars are commonly used to secure the shaft. Housing material for a pillow block is typically made of cast iron or cast steel.

A pintle is a pin or bolt, usually inserted into a gudgeon, which is used as part of a pivot or hinge. Other applications include pintle and lunette ring for towing, and pintle pins securing casters in furniture.

The pitch bearing, also named blade bearing, is a component of modern wind turbines which connect the rotor hub and the rotor blade. The bearing allows the required oscillation to control the loads and power of the wind turbine. The pitch system brings the blade to the desired position by adapting the aerodynamic angle of attack. The pitch system is also used for emergency breaks of the turbine system.

A plain bearing, or more commonly sliding contact bearing and slide bearing, is the simplest type of bearing, comprising just a bearing surface and no rolling elements. Therefore, the journal slides over the bearing surface. The simplest example of a plain bearing is a shaft rotating in a hole. A simple linear bearing can be a pair of flat surfaces designed to allow motion; e.g., a drawer and the slides it rests on or the ways on the bed of a lathe.
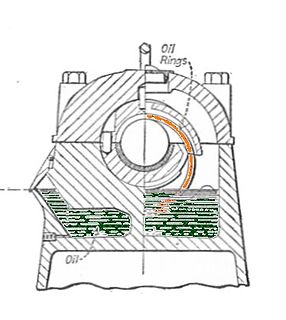
A ring oiler or oil ring is a form of oil-lubrication system for bearings.

Rolamite is a technology for very low friction bearings developed by Sandia National Laboratories in the 1960s. It is the only elementary machine discovered in the twentieth century and can be used in various ways such as a component in switches, thermostats, valves, pumps, and clutches, among others.

A rolling-element bearing, also known as a rolling bearing, is a bearing which carries a load by placing rolling elements between two bearing rings called races. The relative motion of the races causes the rolling elements to roll with very little rolling resistance and with little sliding.

To "slew" means to turn without change of place.

A spherical plain bearing is a bearing that permits angular rotation about a central point in two orthogonal directions. Typically these bearings support a rotating shaft in the bore of the inner ring that must move not only rotationally, but also at an angle.

A spherical roller bearing is a rolling-element bearing that permits rotation with low friction, and permits angular misalignment. Typically these bearings support a rotating shaft in the bore of the inner ring that may be misaligned in respect to the outer ring. The misalignment is possible due to the spherical internal shape of the outer ring and spherical rollers. Despite what their name may imply, spherical roller bearings are not truly spherical in shape. The rolling elements of spherical roller bearings are mainly cylindrical in shape, but have a profile that makes them appear like cylinders that have been slightly over-inflated.

A spherical roller thrust bearing is a rolling-element bearing of thrust type that permits rotation with low friction, and permits angular misalignment. The bearing is designed to take radial loads, and heavy axial loads in one direction. Typically these bearings support a rotating shaft in the bore of the shaft washer that may be misaligned in respect to the housing washer. The misalignment is possible due to the spherical internal shape of the house washer.

Spiral groove bearings are self-acting, or hydrodynamic bearings used to reduce friction and wear without the use of pressurized lubricants. They have this ability due to special patterns of grooves. Spiral groove bearings are self-acting because their own rotation builds up the pressure needed to separate the bearing surfaces. For this reason, they are also contactless bearings.

A thrust bearing is a particular type of rotary bearing. Like other bearings they permanently rotate between parts, but they are designed to support a predominantly axial load.

Sven Gustaf Wingqvist was a Swedish engineer, inventor and industrialist, and one of the founders of Svenska Kullagerfabriken (SKF), one of the world's leading ball bearing and roller bearing makers. Sven Wingqvist invented the multi-row self-aligning ball bearing in 1907.