
A blowout preventer (BOP) is a specialized valve or similar mechanical device, used to seal, control and monitor oil and gas wells to prevent blowouts, the uncontrolled release of crude oil or natural gas from a well. They are usually installed in stacks of other valves.

A borehole is a narrow shaft bored in the ground, either vertically or horizontally. A borehole may be constructed for many different purposes, including the extraction of water, other liquids or gases, as part of a geotechnical investigation, environmental site assessment, mineral exploration, temperature measurement, as a pilot hole for installing piers or underground utilities, for geothermal installations, or for underground storage of unwanted substances, e.g. in carbon capture and storage.

Boring is drilling a hole, tunnel, or well in the earth.

An annular cutter is form of core drill used to create holes in metal. An annular cutter cuts only a groove at the periphery of the hole and leaves a solid core or slug at the center.

The Cameron ram-type blowout preventer was the first successful blowout preventer (BOP) for oil wells. It was developed by James S. Abercrombie and Harry S. Cameron in 1922. The device was issued U.S. Patent 1,569,247 on January 12, 1926. The blowout preventer was designated as a Mechanical Engineering Landmark in 2003.
Casing is a large diameter pipe that is assembled and inserted into a recently drilled section of a borehole. Similar to the bones of a spine protecting the spinal cord, casing is set inside the drilled borehole to protect and support the wellstream. The lower portion is typically held in place with cement. Deeper strings usually are not cemented all the way to the surface, so the weight of the pipe must be partially supported by a casing hanger in the wellhead.
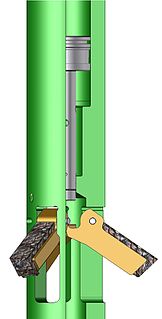
A Casing-Cutter is a device used in petroleum industry to cut a complete section of a casing, a liner or all others tubular components in a well bore. This cutting tool is composed by several cutting blades pivotally mounted on support body. During cutting operations, the cutting blades are gradually deployed outside the support body by hydraulic pressure or mechanical action
Well completion is the process of making a well ready for production after drilling operations. This principally involves preparing the bottom of the hole to the required specifications, running in the production tubing and its associated down hole tools as well as perforating and stimulating as required. Sometimes, the process of running in and cementing the casing is also included. After a well has been drilled, should the drilling fluids be removed, the well would eventually close in upon itself. Casing ensures that this will not happen while also protecting the wellstream from outside incumbents, like water or sand.

A core drill is a drill specifically designed to remove a cylinder of material, much like a hole saw. The material left inside the drill bit is referred to as the core.

A crown block is the stationary section of a block and tackle that contains a set of pulleys or sheaves through which the drill line is threaded or reeved and is opposite and above the traveling block.

Desanders and desilters are solid control equipment with a set of hydrocyclones that separate sand and silt from the drilling fluids in drilling rigs. Desanders are installed on top of the mud tank following the shale shaker and the degasser, but before the desilter. Desander removes the abrasive solids from the drilling fluids which cannot be removed by shakers. Normally the solids diameter for desander to be separated would be 45~74μm, and 15~44μm for desilter.

Differential sticking is a problem that occurs when drilling a well with a greater well bore pressure than formation pressure, as is usually the case. The drill pipe is pressed against the wellbore wall so that part of its circumference will see only reservoir pressure, while the rest will continue to be pushed by wellbore pressure. As a result, the pipe becomes stuck to the wall, and can require millions of pounds of force to remove, which may prove impossible. In many cases the drilling fluid (mud) weight is reduced, thus relieving the pressure difference and releasing the stuck pipe string. Should this option be unavailable, as in sour gas wells, a specialty fishing company is called to retrieve the stuck pipe or 'fish'. Many options exist once a fishing company is on site: oil or nitrogen may be pumped down the well, or the fish may be 'washed over' using a carbide shoe on a string of washpipe. Jarring is not usually attempted with differential sticking due to the massive amount of pressure that holds the pipe in place.

Directional drilling is the practice of drilling non-vertical wells. It can be broken down into four main groups: oilfield directional drilling, utility installation directional drilling, directional boring, and surface in seam (SIS), which horizontally intersects a vertical well target to extract coal bed methane.

A directional well is an oil industry term for an oil well with a borehole that deviates from a vertically straight line. This is normally done with the intention of hitting several target sands, for instance.

In a drilling rig, the drill line is a multi-thread, twisted wire rope that is threaded or reeved through in typically 6 to 12 parts between the traveling block and crown block to facilitate the lowering and lifting of the drill string into and out of the wellbore.

A drill stem test (DST) is a procedure for isolating and testing the pressure, permeability and productive capacity of a geological formation during the drilling of a well. The test is an important measurement of pressure behaviour at the drill stem and is a valuable way of obtaining information on the formation fluid and establishing whether a well has found a commercial hydrocarbon reservoir.

In geotechnical engineering, drilling fluid, also called drilling mud, is used to aid the drilling of boreholes into the earth. Often used while drilling oil and natural gas wells and on exploration drilling rigs, drilling fluids are also used for much simpler boreholes, such as water wells. One of the functions of drilling mud is to carry cuttings out of the hole.

A drilling riser is a conduit that provides a temporary extension of a subsea oil well to a surface drilling facility. Drilling risers are categorised into two types: marine drilling risers used with subsea blowout preventer (BOP) and generally used by floating drilling vessels; and tie-back drilling risers used with a surface BOP and generally deployed from fixed platforms or very stable floating platforms like a spar or tension leg platform (TLP).
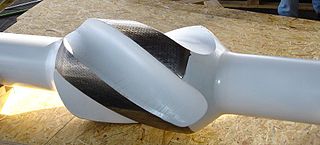
A drilling stabilizer is a piece of downhole equipment used in the bottom hole assembly (BHA) of a drill string. It mechanically stabilizes the BHA in the borehole in order to avoid unintentional sidetracking, vibrations, and ensure the quality of the hole being drilled.

GA Drilling is a high technology company headquartered in Bratislava (Slovakia) with branches in Bristol (UK), Abu Dhabi (UAE) and Houston (USA). The company was founded in 1994 and rebranded as GA Drilling in August 2013. GA Drilling is developing and commercializing PLASMABIT technology platform which provides drilling tool for challenging the most comprehensive energy industry issues. PLASMABIT is based on high-energy electric plasma enabling to operate at a constant speed with no need for changing tool. PLASMABIT applications are primarily addressed to geothermal energy and mining industries. GA Drilling is also active within drilling community through participation at several industry events.

The German Continental Deep Drilling Program, abbreviated as the KTB borehole, was a scientific drilling project carried out from 1987 to 1995 near Windischeschenbach, Bavaria. The main super-deep borehole reached a depth of 9,101 meters in the Earth's continental crust.
A hole opener is a device used to enlarge the borehole during a well drilling operation. It can be positioned either above the drill bit or above a pilot run inside the existing borehole.

Ice drilling allows scientists studying glaciers and ice sheets to gain access to what is beneath the ice, to take measurements along the interior of the ice, and to retrieve samples. Instruments can be placed in the drilled holes to record temperature, pressure, speed, direction of movement, and for other scientific research, such as neutrino detection.

The Kola Superdeep Borehole is the result of a scientific drilling project of the Soviet Union in the Pechengsky District, near the Russian border with Norway, on the Kola Peninsula. The project attempted to drill as deep as possible into the Earth's crust. With a depth of 12,262 metres (40,230 ft), it has been, since 1989, the deepest artificial point on Earth.

A magnetic drilling machine is a portable drilling machine with a magnetic base. It can use twist drill bits, annular cutters, milling cutters, and other rotary cutters. With suitable bits it can also tap threads, ream, and countersink. Its combination of a stable magnetic base and low RPM help resist or reduce torque forces created by large diameter bits. Magnetic drilling machines with reversible motor and variable speed controls can also performa operations like tapping, countersink and reaming. Magnetic drilling machine with cross table base and can also perform light milling.

A drilling riser is a conduit that provides a temporary extension of a subsea oil well to a surface drilling facility. Drilling risers are categorised into two types: marine drilling risers used with subsea blowout preventer (BOP) and generally used by floating drilling vessels; and tie-back drilling risers used with a surface BOP and generally deployed from fixed platforms or very stable floating platforms like a spar or tension leg platform (TLP).

The mousehole is the storage area on a drilling rig where the next joint of drilling pipe is held until needed. This hole is in the floor of the rig, bored into the earth for a short way, and usually lined with a metal casing known as a scabbard.

Effective solids control can be attributed to the overall performance of all the components of the mud systems. Conditioning the drilling fluid with the goal of dramatically lowering maintenance cost, avoiding excessive chemical treatment and maintaining mud systems volume will decrease the chance of equipment failure, unnecessary high mud costs, hole and drilling problems.
Offshore drilling is a mechanical process where a wellbore is drilled below the seabed. It is typically carried out in order to explore for and subsequently extract petroleum which lies in rock formations beneath the seabed. Most commonly, the term is used to describe drilling activities on the continental shelf, though the term can also be applied to drilling in lakes, inshore waters and inland seas.

Offshore oil spill prevention and response is the study and practice of reducing the number of offshore incidents that release oil or hazardous substances into the environment and limiting the amount released during those incidents.
An oil platform, offshore platform, or offshore drilling rig is a large structure with facilities for well drilling to explore, extract, store, and process petroleum and natural gas that lies in rock formations beneath the seabed. Many oil platforms will also contain facilities to accommodate their workforce. Most commonly, oil platforms engage in activities on the continental shelf, though they can also be used in lakes, inshore waters, and inland seas. Depending on the circumstances, the platform may be fixed to the ocean floor, consist of an artificial island, or float. Remote subsea wells may also be connected to a platform by flow lines and by umbilical connections. These sub-sea solutions may consist of one or more subsea wells or of one or more manifold centres for multiple wells.
An oil well is a boring in the Earth that is designed to bring petroleum oil hydrocarbons to the surface. Usually some natural gas is released as associated petroleum gas along with the oil. A well that is designed to produce only gas may be termed a gas well.

Plasma deep drilling technology is one of several different variants of recently explored new drilling technologies which would be able to substitute conventional, contact-based rotary systems. These new technologies, including plasma deep drilling, water jet, hydrothermal spallation or laser, are matter of active research. Only a very small number of companies have embraced plasma-drilling method, e.g. GA Drilling, headquartered in Bratislava, Slovakia.

A Rail Drilling Machine is a type of portable drilling machine specialized for drilling holes in rails. Rail Drilling Machines are also popularly called as Rail Drills, Portable Rail Drill, Rail Core Drilling Machines, etc.
Research Centre for Deep Drilling is high-tech laboratory focused on research and development of new deep drilling concept based on electrical plasma. It was established by GA Drilling, former Geothermal Anywhere company in the premises of Slovak Academy of Sciences in Bratislava, Slovakia. The Research centre was officially opened on 10 October 2010 as a result of long-term activities whose aim is to support the geothermal technology research and development in Slovakia. In October 2012, GA Drilling officially moved from Research Center for Deep Drilling to newly founded GA Drilling Technology Center.
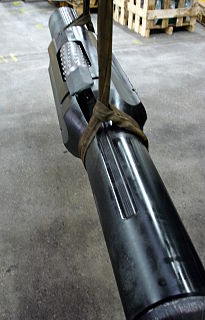
Roller reamers are employed in boring operations for the oil & gas industry. The main function of roller reamers cut earth formations to enlarge the borehole to the desirable size during well drilling operation, which may be the original size of the drill bit in the case where the drill bit wears to be under-gauged. However, even for new drill bits, roller reamers are employed to cut formations because the bit does not always drill a true bore hole and because of slight lateral shifting which is inherent in the drilling operation, which shifting leaves ledges and other distortions. Additionally, the second function of a roller reamer is to keep the drill stem in the center of the hole at the specific position of placement of the roller-reamer. In providing such a function, a reamer is often referred to as a stabilizer. Maintaining the drill stem centered has many beneficial effects, its primary one being minimizing unintentional hole-angle directional drilling.
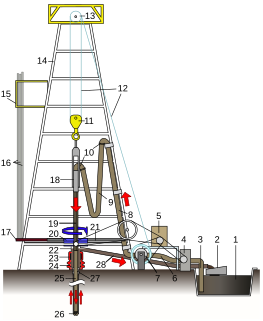
A rotary table is a mechanical device on a drilling rig that provides clockwise rotational force to the drill string to facilitate the process of drilling a borehole. Rotary speed is the number of times the rotary table makes one full revolution in one minute (rpm).

Interferometry examines the general interference phenomena between pairs of signals in order to gain useful information about the subsurface. Seismic interferometry (SI) utilizes the crosscorrelation of signal pairs to reconstruct the impulse response of a given media. Papers by Keiiti Aki (1957), Géza Kunetz, and Jon Claerbout (1968) helped develop the technique for seismic applications and provided the framework upon which modern theory is based.

A semi-submersible platform is a specialised marine vessel used in offshore roles including as offshore drilling rigs, safety vessels, oil production platforms, and heavy lift cranes. They have good ship stability and seakeeping, better than drillships.

A drillship is a merchant vessel designed for use in exploratory offshore drilling of new oil and gas wells or for scientific drilling purposes. In most recent years the vessels are used in deepwater and ultra-deepwater applications, equipped with the latest and most advanced dynamic positioning systems.

The Sidoarjo mud flow is the result of an erupting mud volcano in the subdistrict of Porong, Sidoarjo in East Java, Indonesia that has been in eruption since May 2006. It is the biggest mud volcano in the world; responsibility for it was credited to the blowout of a natural gas well drilled by PT Lapindo Brantas, although some scientists and company officials contend it was caused by a distant earthquake.
A stand is two or three joints of drill pipe connected and stood in the derrick vertically, usually while tripping pipe. A stand of collars is similar, only made up of collars and a collar head. The collar head is screwed into the collar to allow it to be picked up by the elevators.

A Swivel is a mechanical device used on a drilling rig that hangs directly under the traveling block and directly above the kelly drive, that provides the ability for the kelly to rotate while allowing the traveling block to remain in a stationary rotational position while simultaneously allowing the introduction of drilling fluid into the drill string.

A tensioner is a device that applies a force to create or maintain tension. The force may be applied parallel to, as in the case of a hydraulic bolt tensioner, or perpendicular to, as in the case of a spring-loaded bicycle chain tensioner, the tension it creates. The force may be generated by a fixed displacement, as in the case of an eccentric bicycle bottom bracket, which must be adjusted as parts wear, or by stretching or compressing a spring, as in the case of a spring-loaded bicycle chain tensioner; by changing the volume of a gas, as in the case of a marine riser tensioner; by hydraulic pressure, as in the case of a hydraulic bolt tensioner; or by gravity acting on a suspended mass, as in the case of a chair lift cable tensioner. In the power sector, the tensioner is a machine for maintaining constant tension of the conductors during work of hanging the transmission network..

A traveling block is the freely moving section of a block and tackle that contains a set of pulleys or sheaves through which the drill line is threaded or reeved and is opposite the crown block.
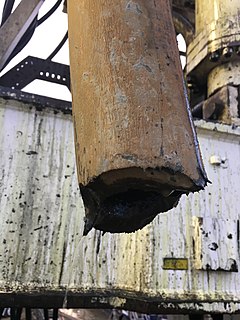
Tripping pipe is the physical act of pulling the drill string out of the wellbore and then running it back in. This is done by physically breaking out or disconnecting every other 2 or 3 joints of drill pipe at a time and racking them vertically in the derrick. When feasible the driller will start each successive trip on a different "break" so that after several trips fresh pipe dope will have been applied to every segment of the drill string.
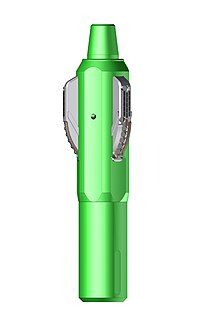
An underreamer is a device used to enlarge the borehole below an existing casing or restriction, during a well drilling operation. It can be positioned either above the drill bit or above a pilot assembly run inside the existing borehole.

Well drilling is the process of drilling a hole in the ground for the extraction of a natural resource such as ground water, brine, natural gas, or petroleum, for the injection of a fluid from surface to a subsurface reservoir or for subsurface formations evaluation or monitoring. Drilling for the exploration of the nature of the material underground is best described as borehole drilling.