
Fracture mechanics is the field of mechanics concerned with the study of the propagation of cracks in materials. It uses methods of analytical solid mechanics to calculate the driving force on a crack and those of experimental solid mechanics to characterize the material's resistance to fracture.

The alkali–silica reaction (ASR), more commonly known as "concrete cancer", is a deleterious swelling reaction that occurs over time in concrete between the highly alkaline cement paste and the reactive amorphous silica found in many common aggregates, given sufficient moisture.
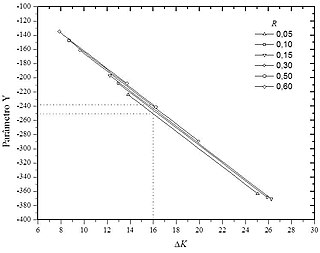
The alpha-beta model is a mathematical equation used to describe the velocity of fatigue crack growth, da / dN, as a function of a constant amplitude load driving force ΔK where its constants α and β are obtained through a semi-empirical process. Originally the alpha-beta model was developed and tested from data generated in tests using commercial grade Titanium and Aluminium Alloy 2524-T3 both the structural materials of great interest aeronautical. This model is applied in two situations: the individual that conforms to the experimental data of a single test and can be compared to Paris' law; and the generalized one that tries to represent in a bi-parametric way the effects of R - ratio between the tensions intensity, minimum and maximum - for a set of tests in the same material.

A cascade chart is tool that can be used in damage tolerance analysis to determine the proper inspection interval, based on reliability analysis, considering all the context uncertainties. The chart is called a "cascade chart" because the scatter of data points and downward curvature resembles a waterfall or cascade. This name was first introduced by Dr. Alberto W Mello in his work "Reliability prediction for structures under cyclic loads and recurring inspections". Materials subject to cyclic loads, as shown in the graph on the right, may form and propagate cracks over time due to fatigue. Therefore, it is essential to determine a reliable inspection interval. There are numerous factors that must be considered to determine this inspection interval. The non-destructive inspection (NDI) technique must have a high probability of detecting a crack in the material. If missed, a crack may lead the structure to a catastrophic failure before the next inspection. On the other hand, the inspection interval cannot be too frequent that the structure's maintenance is no longer profitable.
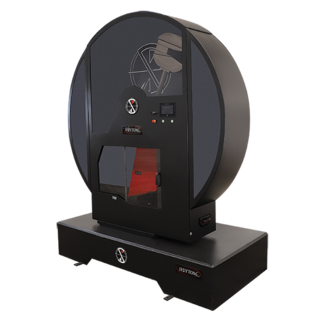
The Charpy impact test, also known as the Charpy V-notch test, is a standardized high strain-rate test which determines the amount of energy absorbed by a material during fracture. Absorbed energy is a measure of the material's notch toughness. It is widely used in industry, since it is easy to prepare and conduct and results can be obtained quickly and cheaply. A disadvantage is that some results are only comparative. The test was pivotal in understanding the fracture problems of ships during World War II.

The cohesive zone model (CZM) is a model in fracture mechanics in which fracture formation is regarded as a gradual phenomenon in which separation of the surfaces involved in the crack takes place across an extended crack tip, or cohesive zone, and is resisted by cohesive tractions. The origin of this model can be traced back to the early sixties by Barenblatt (1962) and Dugdale (1960) to represent nonlinear processes located at the front of a pre-existent crack.
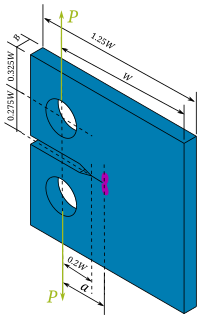
A compact tension specimen (CT) is a type of standard notched specimen in accordance with ASTM and ISO standards. Compact tension specimens are used extensively in the area of fracture mechanics and corrosion testing, in order to establish fracture toughness and fatigue crack growth data for a material.

A crack growth equation is used for calculating the size of a fatigue crack growing from cyclic loads. The growth of fatigue cracks can result in catastrophic failure, particularly in the case of aircraft. A crack growth equation can be used to ensure safety, both in the design phase and during operation, by predicting the size of cracks. In critical structure, loads can be recorded and used to predict the size of cracks to ensure maintenance or retirement occurs prior to any of the cracks failing.

Critical plane analysis refers to the analysis of stresses or strains as they are experienced by a particular plane in a material, as well as the identification of which plane is likely to experience the most extreme damage. Critical plane analysis is widely used in engineering to account for the effects of cyclic, multiaxial load histories on the fatigue life of materials and structures. When a structure is under cyclic multiaxial loading, it is necessary to use multiaxial fatigue criteria that account for the multiaxial loading. If the cyclic multiaxial loading is nonproportional it is mandatory to use a proper multiaxial fatigue criteria. The multiaxial criteria based on the Critical Plane Method are the most effective criteria.

Crocodile cracking, also called alligator cracking and perhaps misleadingly fatigue cracking, is a common type of distress in asphalt pavement. The following is more closely related to fatigue cracking which is characterized by interconnecting or interlaced cracking in the asphalt layer resembling the hide of a crocodile. Cell sizes can vary in size up to 11.80 inches (300 mm) across, but are typically less than 5.90 inches (150 mm) across. Fatigue cracking is generally a loading failure, but numerous factors can contribute to it. It is often a sign of sub-base failure, poor drainage, or repeated over-loadings. It is important to prevent fatigue cracking, and repair as soon as possible, as advanced cases can be very costly to repair and can lead to formation of potholes or premature pavement failure.

Enamel tufts are hypomineralized ribbon-like structures that run longitudinally to the tooth axis and extend from the dentinoenamel junction (DEJ) one fifth to a third into the enamel. They are called ‘‘tufts’’ due to their wavy look within the enamel microstructure.

In materials science, fatigue is the weakening of a material caused by cyclic loading that results in progressive and localized structural damage and the growth of cracks. Once a fatigue crack has initiated, it will grow a small amount with each loading cycle, typically producing striations on some parts of the fracture surface. The crack will continue to grow until it reaches a critical size, which occurs when the stress intensity factor of the crack exceeds the fracture toughness of the material, producing rapid propagation and typically complete fracture of the structure.
The fatigue limit, also known as the endurance limit or fatigue strength, is the stress level below which an infinite number of loading cycles can be applied to a material without causing fatigue failure.

Fatigue testing is a specialised form of mechanical testing that is performed by applying cyclic loading to a coupon or structure. These tests are used either to generate fatigue life and crack growth data, identify critical locations or demonstrate the safety of a structure that may be susceptible to fatigue. Fatigue tests are used on a range components from coupons through to full size test articles such as automobiles and aircraft.

Fractography is the study of the fracture surfaces of materials. Fractographic methods are routinely used to determine the cause of failure in engineering structures, especially in product failure and the practice of forensic engineering or failure analysis. In material science research, fractography is used to develop and evaluate theoretical models of crack growth behavior.

In materials science, fracture toughness is the critical stress intensity factor of a sharp crack where propagation of the crack suddenly becomes rapid and unlimited. A component's thickness affects the constraint conditions at the tip of a crack with thin components having plane stress conditions and thick components having plane strain conditions. Plane strain conditions give the lowest fracture toughness value which is a material property. The critical value of stress intensity factor in mode I loading measured under plane strain conditions is known as the plane strain fracture toughness, denoted . When a test fails to meet the thickness and other test requirements that are in place to ensure plane strain conditions, the fracture toughness value produced is given the designation . Fracture toughness is a quantitative way of expressing a material's resistance to crack propagation and standard values for a given material are generally available.

A material is said to be frangible if through deformation it tends to break up into fragments, rather than deforming elastically and retaining its cohesion as a single object. Common crackers are examples of frangible materials, while fresh bread, which deforms plastically, is not frangible.

In mechanics, an impact is a high force or shock applied over a short time period when two or more bodies collide. Such a force or acceleration usually has a greater effect than a lower force applied over a proportionally longer period. The effect depends critically on the relative velocity of the bodies to one another.
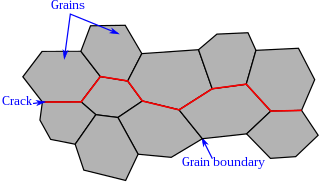
Intergranular fracture occurs when a crack propagates along the grain boundaries of a material, usually when these grain boundaries are weakened. The more commonly seen transgranular fracture, occurs when the crack grows through the material grains. As an analogy, in a wall of bricks, intergranular fracture would correspond to a fracture that takes place in the mortar that keeps the bricks together.

The Izod impact strength test is an ASTM standard method of determining the impact resistance of materials. A pivoting arm is raised to a specific height and then released. The arm swings down hitting a notched sample, breaking the specimen. The energy absorbed by the sample is calculated from the height the arm swings to after hitting the sample. A notched sample is generally used to determine impact energy and notch sensitivity.
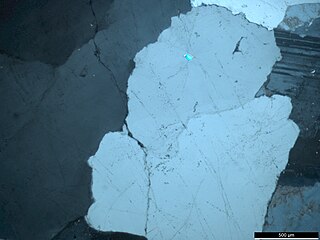
Microcracks in rock, also known as microfractures and cracks, are spaces in rock with the longest length of 1000 μm and the other two dimensions of 10 μm. In general, the ratio of width to length of microcracks is between 10−3 to 10−5.

Microvoid coalescence (MVC) is a high energy microscopic fracture mechanism observed in the majority of metallic alloys and in some engineering plastics.

The Palmqvist method, or the Palmqvist toughness test, is a common method to determine the fracture toughness for cemented carbides. In this case, the materials fracture toughness is represented by the critical stress intensity factor KIc.

Paris' law is a crack growth equation that gives the rate of growth of a fatigue crack. The stress intensity factor characterises the load around a crack tip and the rate of crack growth is experimentally shown to be a function of the range of stress intensity seen in a loading cycle. The Paris equation is

Peridynamics is a formulation of continuum mechanics that is oriented toward deformations with discontinuities, especially fractures.

The rainflow-counting algorithm is used in the analysis of fatigue data in order to reduce a spectrum of varying stress into an equivalent set of simple stress reversals. The method successively extracts the smaller interruption cycles from a sequence, which models the material memory effect seen with stress-strain hysteresis cycles. This simplification allows the fatigue life of a component to be determined for each rainflow cycle using either Miner's rule to calculate the fatigue damage, or in a crack growth equation to calculate the crack increment. The algorithm was developed by Tatsuo Endo and M. Matsuishi in 1968.

According to the classical theories of elastic or plastic structures made from a material with non-random strength (ft), the nominal strength (σN) of a structure is independent of the structure size (D) when geometrically similar structures are considered. Any deviation from this property is called the size effect. For example, conventional strength of materials predicts that a large beam and a tiny beam will fail at the same stress if they are made of the same material. In the real world, because of size effects, a larger beam will fail at a lower stress than a smaller beam.
Stress corrosion cracking (SCC) is the growth of crack formation in a corrosive environment. It can lead to unexpected and sudden failure of normally ductile metal alloys subjected to a tensile stress, especially at elevated temperature. SCC is highly chemically specific in that certain alloys are likely to undergo SCC only when exposed to a small number of chemical environments. The chemical environment that causes SCC for a given alloy is often one which is only mildly corrosive to the metal. Hence, metal parts with severe SCC can appear bright and shiny, while being filled with microscopic cracks. This factor makes it common for SCC to go undetected prior to failure. SCC often progresses rapidly, and is more common among alloys than pure metals. The specific environment is of crucial importance, and only very small concentrations of certain highly active chemicals are needed to produce catastrophic cracking, often leading to devastating and unexpected failure.

The stress intensity factor, , is used in fracture mechanics to predict the stress state near the tip of a crack or notch caused by a remote load or residual stresses. It is a theoretical construct usually applied to a homogeneous, linear elastic material and is useful for providing a failure criterion for brittle materials, and is a critical technique in the discipline of damage tolerance. The concept can also be applied to materials that exhibit small-scale yielding at a crack tip.

Striations are marks produced on the fracture surface that show the incremental growth of a fatigue crack. A striation marks the position of the crack tip at the time it was made. The term striation generally refers to ductile striations which are rounded bands on the fracture surface separated by depressions or fissures and can have the same appearance on both sides of the mating surfaces of the fatigue crack. Although some research has suggested that many loading cycles are required to form a single striation, it is now generally thought that each striation is the result of a single loading cycle.
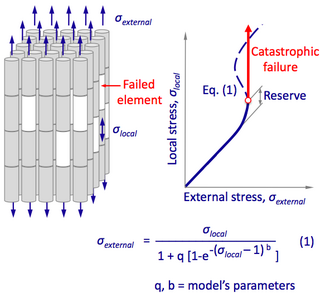
Structural fracture mechanics is the field of structural engineering concerned with the study of load-carrying structures that includes one or several failed or damaged components. It uses methods of analytical solid mechanics, structural engineering, safety engineering, probability theory, and catastrophe theory to calculate the load and stress in the structural components and analyze the safety of a damaged structure.

Tribo-Fatigue is a subdiscipline of mechanics, which studies wear-fatigue damage (WFD) in and the fracture of tribo-fatigue systems. The field was founded at the junction of tribology, and mechanics of fatigue damage and fracture in materials and structural elements.

Vibration fatigue is a mechanical engineering term describing material fatigue, caused by forced vibration of random nature. An excited structure responds according to its natural-dynamics modes, which results in a dynamic stress load in the material points. The process of material fatigue is thus governed largely by the shape of the excitation profile and the response it produces. As the profiles of excitation and response are preferably analyzed in the frequency domain it is practical to use fatigue life evaluation methods, that can operate on the data in frequency-domain, such as power spectral density (PSD).

Widespread fatigue damage (WFD) in a structure is characterised by the simultaneous presence of fatigue cracks at multiple points that are of sufficient size and density that while individually they may be acceptable, link-up of the cracks could suddenly occur and the structure could fail. For example, small fatigue cracks developing along a row of fastener holes can coalesce increasing the stress on adjacent cracked sites increasing the rate of growth of those cracks. The objective of a designer is to determine when large numbers of small cracks could degrade the joint strength to an unacceptable level. The in-flight loss of part of the fuselage from Aloha Airlines Flight 243 was attributed to multi-site fatigue damage.