
Corrosion is a natural process that converts a refined metal into a more chemically stable form such as oxide, hydroxide, or sulfide. It is the gradual destruction of materials by chemical and/or electrochemical reaction with their environment. Corrosion engineering is the field dedicated to controlling and preventing corrosion.

Bacterial anaerobic corrosion is a bacterially-induced oxidation of metals.

Chalconatronite is a carbonate mineral and rare secondary copper mineral that contains copper, sodium, carbon, oxygen, and hydrogen, its chemical formula is Na2Cu(CO3)2•3(H2O). Chalconatronite is partially soluble in water, and only decomposes, although chalconatronite is soluble while cold, in dilute acids. The name comes from the mineral's compounds, copper ("chalcos" in Greek) and natron, naturally forming sodium carbonate. The mineral is thought to be formed by water carrying alkali carbonates (possibly from soil) reacting with bronze. Similar minerals include malachite, azurite, and other copper carbonates. Chalconatronite has also been found and recorded in Australia, Germany, and Colorado.

Concrete degradation may have various causes. Concrete can be damaged by fire, aggregate expansion, sea water effects, bacterial corrosion, calcium leaching, physical damage and chemical damage. This process adversely affects concrete exposed to these damaging stimuli.

Copper has earned a respected place in the related fields of architecture, building construction, and interior design. From cathedrals to castles and from homes to offices, copper is used for a variety of architectural elements, including roofs, flashings, gutters, downspouts, domes, spires, vaults, wall cladding, and building expansion joints.
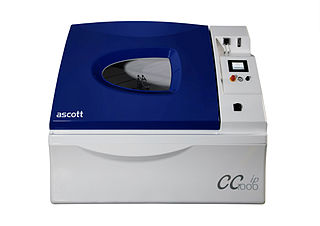
Cyclic Corrosion Testing (CCT) has evolved in recent years, largely within the automotive industry, as a way of accelerating real-world corrosion failures, under laboratory controlled conditions. As the name implies, the test comprises different climates which are cycled automatically so the samples under test undergo the same sort of changing environment that would be encountered in the natural world. The intention being to bring about the type of failure that might occur naturally, but more quickly i.e. accelerated. By doing this manufacturers and suppliers can predict, more accurately, the service life expectancy of their products.

The dithionite anion ([S2O4]2−), is an oxoanion of sulfur. It is commonly encountered as colorless salts.

Ferroxyl indicator is a solution containing potassium hexacyanoferrate(III) and phenolphthalein. It turns blue in the presence of Fe2+ ions, pink in the presence of hydroxide ions, it can be used to detect metal oxidation. It is often used to detect rusting in various situations.

Fretting refers to wear and sometimes corrosion damage at the asperities of contact surfaces. This damage is induced under load and in the presence of repeated relative surface motion, as induced for example by vibration. The ASM Handbook on Fatigue and Fracture defines fretting as: "A special wear process that occurs at the contact area between two materials under load and subject to minute relative motion by vibration or some other force." Fretting tangibly degrades the surface layer quality producing increased surface roughness and micropits, which reduces the fatigue strength of the components.

A galvanic cell or voltaic cell, named after Luigi Galvani or Alessandro Volta, respectively, is an electrochemical cell that derives electrical energy from spontaneous redox reactions taking place within the cell. It generally consists of two different metals immersed in electrolytes, or of individual half-cells with different metals and their ions in solution connected by a salt bridge or separated by a porous membrane.

Galvanic corrosion is an electrochemical process in which one metal corrodes preferentially when it is in electrical contact with another, in the presence of an electrolyte. A similar galvanic reaction is exploited in primary cells to generate a useful electrical voltage to power portable devices.

A gold–aluminium intermetallic is an intermetallic compound of gold and aluminium that occurs at contacts between the two metals.

Green rust is a generic name for various green crystalline chemical compounds containing iron(II) and iron(III) cations, the hydroxide (HO−) anion, and another anion such as carbonate (CO2−3), chloride (Cl−), or sulfate (SO2−4), in a layered double hydroxide structure. The most studied varieties arecarbonate green rust - GR(CO2−3): [Fe2+4Fe3+2(HO−)12]2+ · [CO2−3·2H2O]2−. chloride green rust - GR(Cl−): [Fe2+3Fe3+(HO−)8]+ · [Cl−·nH2O]−. sulfate green rust - GR(SO2−4): [Fe2+4Fe3+2(HO−)12]2+ · [SO2−4·2H2O]2−.

High-temperature corrosion is a mechanism of corrosion that takes place in gas turbines, diesel engines, furnaces or other machinery coming in contact with hot gas containing certain contaminants. Fuel sometimes contains vanadium compounds or sulfates which can form compounds during combustion having a low melting point. These liquid melted salts are strongly corrosive for stainless steel and other alloys normally inert against the corrosion and high temperatures. Other high-temperature corrosions include high-temperature oxidation, sulfidation and carbonization. High temperature oxidation and other corrosion types are commonly modelled using the Deal-Grove model to account for diffusion and reaction processes.

Hydrogen embrittlement (HE) also known as hydrogen assisted cracking (HAC) and hydrogen-induced cracking (HIC), describes the embrittling of metal after being exposed to hydrogen. It is a complex process that is not completely understood because of the variety and complexity of mechanisms that can lead to embrittlement. Mechanisms that have been proposed to explain embrittlement include the formation of brittle hydrides, the creation of voids that can lead to bubbles and pressure build-up within a material and enhanced decohesion or localised plasticity that assist in the propagation of cracks.
Intergranular corrosion (IGC), also known as intergranular attack (IGA), is a form of corrosion where the boundaries of crystallites of the material are more susceptible to corrosion than their insides.
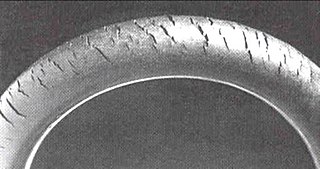
Cracks can be formed in many different elastomers by ozone attack, and the characteristic form of attack of vulnerable rubbers is known as ozone cracking. The problem was formerly very common, especially in tires, but is now rarely seen in those products owing to preventive measures.

Panel edge staining is a naturally occurring problem that occurs to anodized aluminium and stainless steel panelling and façades. It is semi-permanent staining that dulls the panel or façade's surface, reducing the natural lustre and shine produced by the anodizing processes used on the aluminium. Panel edge staining may also appear on powder coated aluminium, painted aluminium, stainless steel and titanium surfaces.

Pitting corrosion, or pitting, is a form of extremely localized corrosion that leads to the creation of small holes in the metal. The driving power for pitting corrosion is the depassivation of a small area, which becomes anodic while an unknown but potentially vast area becomes cathodic, leading to very localized galvanic corrosion. The corrosion penetrates the mass of the metal, with a limited diffusion of ions.

Polysulfides are a class of chemical compounds containing chains of sulfur atoms. There are two main classes of polysulfides: anions and organic polysulfides. Anions have the general formula S2−n. These anions are the conjugate bases of the hydrogen polysulfides H2Sn. Organic polysulfides generally have the formulae RSnR, where R = alkyl or aryl.

Rust is an iron oxide, a usually reddish brown oxide formed by the reaction of iron and oxygen in the presence of water or air moisture. Rust consists of hydrated iron(III) oxides Fe2O3·nH2O and iron(III) oxide-hydroxide (FeO(OH), Fe(OH)3). It is typically associated with the corrosion of refined iron.
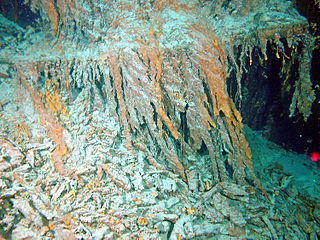
A rusticle is a formation of rust similar to an icicle or stalactite in appearance that occurs deep underwater when wrought iron oxidizes. They may be familiar from underwater photographs of shipwrecks, such as the RMS Titanic and the German battleship Bismarck. They have also been found in the #3 turret, 8-inch gun turret on the stern remains in place of the USS Indianapolis. Rusticles are created by microbes that consume iron.

The Schikorr reaction formally describes the conversion of the iron(II) hydroxide (Fe(OH)2) into iron(II,III) oxide (Fe3O4). This transformation reaction was first studied by Gerhard Schikorr. The global reaction follows:

Season cracking is a form of stress-corrosion cracking of brass cartridge cases originally reported from British forces in India. During the monsoon season, military activity was temporarily reduced, and ammunition was stored in stables until the dry weather returned. Many brass cartridges were subsequently found to be cracked, especially where the case was crimped to the bullet. It was not until 1921 that the phenomenon was explained by Moor, Beckinsale and Mallinson: ammonia from horse urine, combined with the residual stress in the cold-drawn metal of the cartridges, was responsible for the cracking.

Spall are flakes of a material that are broken off a larger solid body and can be produced by a variety of mechanisms, including as a result of projectile impact, corrosion, weathering, cavitation, or excessive rolling pressure. Spalling and spallation both describe the process of surface failure in which spall is shed.
Stress corrosion cracking (SCC) is the growth of crack formation in a corrosive environment. It can lead to unexpected and sudden failure of normally ductile metal alloys subjected to a tensile stress, especially at elevated temperature. SCC is highly chemically specific in that certain alloys are likely to undergo SCC only when exposed to a small number of chemical environments. The chemical environment that causes SCC for a given alloy is often one which is only mildly corrosive to the metal. Hence, metal parts with severe SCC can appear bright and shiny, while being filled with microscopic cracks. This factor makes it common for SCC to go undetected prior to failure. SCC often progresses rapidly, and is more common among alloys than pure metals. The specific environment is of crucial importance, and only very small concentrations of certain highly active chemicals are needed to produce catastrophic cracking, often leading to devastating and unexpected failure.

Sulfide (British English also sulphide) is an inorganic anion of sulfur with the chemical formula S2− or a compound containing one or more S2− ions. Solutions of sulfide salts are corrosive. Sulfide also refers to chemical compounds large families of inorganic and organic compounds, e.g. lead sulfide and dimethyl sulfide. Hydrogen sulfide (H2S) and bisulfide (SH−) are the conjugate acids of sulfide.

Tarnish is a thin layer of corrosion that forms over copper, brass, aluminum, magnesium, neodymium and other similar metals as their outermost layer undergoes a chemical reaction. Tarnish does not always result from the sole effects of oxygen in the air. For example, silver needs hydrogen sulfide to tarnish, although it may tarnish with oxygen over time. It often appears as a dull, gray or black film or coating over metal. Tarnish is a surface phenomenon that is self-limiting, unlike rust. Only the top few layers of the metal react, and the layer of tarnish seals and protects the underlying layers from reacting.

The tetrathionate anion,S4O2−6, is a sulfur oxoanion derived from the compound tetrathionic acid, H2S4O6. Two of the sulfur atoms present in the ion are in oxidation state 0 and two are in oxidation state +5. Alternatively, the compound can be viewed as the adduct resulting from the binding of S2−2 to SO3. Tetrathionate is one of the polythionates, a family of anions with the formula [Sn(SO3)2]2−. Its IUPAC name is 2-(dithioperoxy)disulfate, and the name of its corresponding acid is 2-(dithioperoxy)disulfuric acid. The Chemical Abstracts Service identifies tetrathionate by the CAS Number 15536-54-6.

Thiosulfate is an oxyanion of sulfur.

Tin pest is an autocatalytic, allotropic transformation of the element tin, which causes deterioration of tin objects at low temperatures. Tin pest has also been called tin disease, tin blight or tin leprosy.

Tribocorrosion is a material degradation process due to the combined effect of corrosion and wear. The name tribocorrosion expresses the underlying disciplines of tribology and corrosion. Tribology is concerned with the study of friction, lubrication and wear and corrosion is concerned with the chemical and electrochemical interactions between a material, normally a metal, and its environment. As a field of research tribocorrosion is relatively new, but tribocorrosion phenomena have been around ever since machines and installations are being used.

Zinc pest, also known as zinc rot and mazak rot, is a destructive, intercrystalline corrosion process of zinc alloys containing lead impurities. While impurities of the alloy are the primary cause of the problem, environmental conditions such as high humidity may accelerate the process.